Key Considerations in Selective Soldering for SMT
If you happen to be in the market for selective soldering systems, there are lots of choices. However, before settling on a particular system or supplier, consider the impact of lead-free.
The term "selective soldering" is used when components are added to a partially assembled SMT board. Therefore, selection of selective soldering equipment will vary based on the type of component (through-hole or SMT) to be added to a partially assembled SMT board (full SMT or mixed technology).
Selective soldering of through-hole components. While SMT is the predominant technology today, through-hole will not go away for a long time, even though it is used as a small percentage of total components on a board. So the need for selective soldering of through-hole components will increase as the industry tries to get away from hand and wave soldering to achieve consistent quality.
Selective soldering for through-hole components is a fast-growing segment of the electronics equipment market. In addition to throughput, equipment footprint and cost, which are generally considered when selecting a type of machine, the impact of lead-free on selective soldering equipment selection also must be considered. For example, if you plan to buy only one sel-ective soldering system, it may not be easy to change from tin-lead to lead-free if any of the various configurations of wavesoldering systems are purchased. Since the industry will be using both lead-free and tin-lead alloys between now and at least June 30, 2006, dual use of the machine must be considered.
Some companies want to only purchase a wavesolder pot for lead-free. This approach is cheaper but not advisable, since the fingers of the conveyor will be the source of lead contamination in lead-free solder joints. Changing a hot solder pot from tin-lead to lead-free and vice versa also raises safety concerns for the operator. Selective laser soldering systems can change from lead-free to tin-lead in less than two minutes. Unless you plan to buy separate selective soldering systems, laser soldering systems may make more sense because of their flexibility in quick changeover. In addition, closed-loop temperature monitoring, CAD input for solder fillet requirements and ability to selectively solder fine-pitch, through-hole components without fixtures are other key advantages of laser soldering systems.
Selective soldering of SMT components. While many options are available for automated selective soldering of through-hole components, not too many exist for automated selective soldering of SMT ones. A good example of the need for automated selective soldering is assembly of missing components, planned or unplanned. There has been no equipment to address the issue of missing com-ponents. Manual soldering has been the only option until laser systems came on the market.
Electronics products are growing smaller and lighter every day by the packing of components on a board ever closer together, so much so that it is almost impossible to selectively solder these boards. Cell phones, PDAs, laptops and even desktops are good examples of tightly packed assemblies. Using diode lasers, selective soldering in tight spaces is a key benefit of laser soldering systems.
Traditional SMT assembly involves a high-speed line that produces assemblies at high speed. But when something goes wrong, the same SMT line will produce scrap at the same high speed. When this happens, an automated selective laser soldering system will not impact the adjacent components. Ability to solder moisture-sensitive components without baking provides faster cycle time, a key concern in a production environment. Laser systems also address some emerging technology issues, such as assembly of optoelectronic components that cannot be subjected to reflow temperatures. Optoelectronics is an emerging technology and its use is expected to grow rapidly in the near future.
Even though there is not complete unanimity on the right lead-free composition, as is the case with eutectic tin-lead solder, all lead-free solders have a melting point approximately 40°C higher than that of tin-lead (179° or 183°C). To implement lead-free, higher-temperature board and component package materials must be used, which will be more expensive than current materials. New equipment also may be needed to accommodate high-temperature lead-free solders. Laser soldering systems can address these issues without the need for high-temperature circuit board materials or any modification.
Ray P. Prasad is an SMT Editorial Advisory Board member and author of the textbook Surface Mount Technology: Principles and Practice. Additionally, he is president of BeamWorks Inc. and founder of the Ray Prasad Consultancy Group. Contact him at www.rayprasad.com.
The term "selective soldering" is used when components are added to a partially assembled SMT board. Therefore, selection of selective soldering equipment will vary based on the type of component (through-hole or SMT) to be added to a partially assembled SMT board (full SMT or mixed technology).
Selective soldering of through-hole components. While SMT is the predominant technology today, through-hole will not go away for a long time, even though it is used as a small percentage of total components on a board. So the need for selective soldering of through-hole components will increase as the industry tries to get away from hand and wave soldering to achieve consistent quality.
Selective soldering for through-hole components is a fast-growing segment of the electronics equipment market. In addition to throughput, equipment footprint and cost, which are generally considered when selecting a type of machine, the impact of lead-free on selective soldering equipment selection also must be considered. For example, if you plan to buy only one sel-ective soldering system, it may not be easy to change from tin-lead to lead-free if any of the various configurations of wavesoldering systems are purchased. Since the industry will be using both lead-free and tin-lead alloys between now and at least June 30, 2006, dual use of the machine must be considered.
Some companies want to only purchase a wavesolder pot for lead-free. This approach is cheaper but not advisable, since the fingers of the conveyor will be the source of lead contamination in lead-free solder joints. Changing a hot solder pot from tin-lead to lead-free and vice versa also raises safety concerns for the operator. Selective laser soldering systems can change from lead-free to tin-lead in less than two minutes. Unless you plan to buy separate selective soldering systems, laser soldering systems may make more sense because of their flexibility in quick changeover. In addition, closed-loop temperature monitoring, CAD input for solder fillet requirements and ability to selectively solder fine-pitch, through-hole components without fixtures are other key advantages of laser soldering systems.
Selective soldering of SMT components. While many options are available for automated selective soldering of through-hole components, not too many exist for automated selective soldering of SMT ones. A good example of the need for automated selective soldering is assembly of missing components, planned or unplanned. There has been no equipment to address the issue of missing com-ponents. Manual soldering has been the only option until laser systems came on the market.
Electronics products are growing smaller and lighter every day by the packing of components on a board ever closer together, so much so that it is almost impossible to selectively solder these boards. Cell phones, PDAs, laptops and even desktops are good examples of tightly packed assemblies. Using diode lasers, selective soldering in tight spaces is a key benefit of laser soldering systems.
Traditional SMT assembly involves a high-speed line that produces assemblies at high speed. But when something goes wrong, the same SMT line will produce scrap at the same high speed. When this happens, an automated selective laser soldering system will not impact the adjacent components. Ability to solder moisture-sensitive components without baking provides faster cycle time, a key concern in a production environment. Laser systems also address some emerging technology issues, such as assembly of optoelectronic components that cannot be subjected to reflow temperatures. Optoelectronics is an emerging technology and its use is expected to grow rapidly in the near future.
Even though there is not complete unanimity on the right lead-free composition, as is the case with eutectic tin-lead solder, all lead-free solders have a melting point approximately 40°C higher than that of tin-lead (179° or 183°C). To implement lead-free, higher-temperature board and component package materials must be used, which will be more expensive than current materials. New equipment also may be needed to accommodate high-temperature lead-free solders. Laser soldering systems can address these issues without the need for high-temperature circuit board materials or any modification.
Ray P. Prasad is an SMT Editorial Advisory Board member and author of the textbook Surface Mount Technology: Principles and Practice. Additionally, he is president of BeamWorks Inc. and founder of the Ray Prasad Consultancy Group. Contact him at www.rayprasad.com.
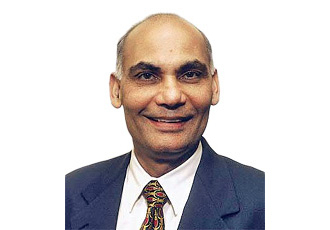
Registration is Open for SMT Course
Ray Prasad will be teaching his flagship SMT course: