Lead Free Soldering Quiz
Test your understanding of SMT with the questions below. If you have trouble answering some of the questions, you may benefit from the Lead Free course taught by Mr. Ray Prasad.
Section 1
1-1 What is the definition of Lead Free?
1-2 How many categories of Lead free Readiness are there? Name Them
1-3 In the US, which material is recycled more: Batteries, newspapers, aluminum cans, glass bottles.
1-4 True or False: RoHS is the legislation for elimination of lead only.
1-5 When was the effective date for the RoHS legislation.
1-6 What does WEEE stand for and what does it control? When did it become effective?
1-7 List the names of some materials that are exempt from RoHS.
1-8 What would be the most significant item that will limit your ability to convert products to lead free, despite your company's full commitment of resources and people?
1-9 True or False: One can currently buy lead free products on the market today. Are they totally lead free?
1-10 Which is the main driver for lead free products today: Legislation or Competitive Pressure.
1-11 True or False: When did China RoHS become effective?. Is RoHS directive by China is less or more restrictive than EU?
1-12 True of False: In USA there is no legal requirement for RoHS compliance
1-13 List the names of some Industry Consortias working towards lead-free implementation.
1-14 List the new capital equipment that you will need for lead free conversion.
1-17 True or False: Lead Metal is cheaper than Tin Metal
1-18 What are the benefits of maintaining dual manufacturing lines, i.e., Lead-free and Tin-Lead?
1-19 What does the WEEE man represent?
1-20 Which category is the largest when doing the calculations for the WEEE man
1-21 Describe the Symbol for Marking of EEE for Separate Collection?
1-22 How much mercury is allowed in EU directive?
1-18 True or False: California has passed the RoHS directive as EU. When did it effective?
Section 2
2-1 What are the key requirements for selecting a lead free solder?
2-2 What is the definition of a eutectic composition?
2-3 Give some examples if binary solder systems which exhibit eutectic behavior.
2-4 How do you find a eutectic composition on a binary phase diagram?
2-5 What are the advantages of Bismuth containing solders?
2-6 What are the disadvantages of Bismuth Containing solders?
2-7 Why are indium containing solders not preferred as the best choice for lead free solders?
2-8 Tin-zinc eutectic solders have a lower melting point as well as better mechanical properties than SAC solders. Yet, tin-zinc solders are not preferred to SAC solders. Why?
2-9 Besides the high cost of gold, why are gold containing solders not considered for use in lead free soldering?
2-10 What are the compositions of the most popular lead free solder alloys chosen around the world?
2-11 What is the composition of SAC396 alloy?
2-12 Why is the SAC305 composition preferred over SAC405?
2-13 True or False: SAC solders melt completely at a lower temperature than eutectic Sn-Pb solder.
2-14 What is the typical Peak reflow Temperature during the lead free soldering process?
2-15 What are some of the material properties considered when choosing potential lead free solders by the Industry consortia that initially worked on the selection process?
2-16 What is the typical microstructure of the SAC305 alloy?
2-17 What is the typical microstructure of SAC405 alloy and why is it dependant on the cooling rate of the solder joints as they exit the reflow soldering oven?
2-18 True or False: Lead free soldering results in thicker Intermetallic Compounds at the solder to copper land interfaces?
2-19 What are the intermetallic compound compositions that form when SAC solder is reflowed on an OSP coated copper land?
2-20 What are the Intermetallic compounds that form when SAC solder is reflow soldered on an Immersion Silver coated copper land?
2-21 What is the composition of the SN100C Wave Solder lead free alloy and what does it’s manufacturer claim are its advantages over other lead free wave solder alloys?
2-22 Besides SN100C, what are the other wave solder alloys being marketed today? List some advantageous properties of these alloys.
2-23 What is the range of wetting angle that is considered an indication of an excellent quality solder joint?
2-24 True or False: SAC solders have lower wetting angle than eutectic SnPb solders.
2-25 Ture or False: SAC solders typically have a dull look when inspected visually as compared to eutectic SnPb solders.
2-26 True or False: Under low strain conditions, SAC solders are better than SnPb solders when subjected to temperature cycling tests.
2-27 What is the observed damaged mechanism within the microstructure of a SAC BGA solder joint and how does it differ from that of a eutectic SnPb solder joint?
2-28 True or False: For rigid packages such as LCCCs, CBGAs, Resistors, TSOPs, Flip Chips, SnPb solder is better than SAC
2-29 Why has mechanical shock and drop resistance of solders become an important aspect of product reliability recently?
2-30 Why are SAC solders significantly worse than eutectic SnPb solders during mechanical shock and drop tests?
2-31 Why is SAC105 composition better than SAC305 for mechanical shock and drop resistance? What are the disadvantaged of SAC105 with respect to the SAC305 and SAC405 compositions?
2-32 What is Pad Cratering and when does it occur?
2-33 Why is Pad Cratering more prevalent when SAC solders are used than when SnPb solders are used?
2-34 What are some ways of mitigating Pad Cratering?
2-35 What is the difference between Planar MicroVoids and Micro Via Voids?
2-36 True or False: Shrink hole voids are present in solder joints irrespective of the solder composition
2-37 Is there a consensus on the testing protocol (ramp rate and dwell times at temperature extremes) for thermal cycling of lead free board products?
2-38 Does a longer dwell time at the temperature extremes during thermal cycling, enhance or diminish SAC alloy solder joint life?.
2-39 True or False: Wetting time increases with Increasing Temperature for Lead Free Alloys
2-40 True or False: IMC Microvoids can be minimized by optimizing the reflow soldering profile
2-41 Describe Macrovoids. How do they differ from Planar Microvoids.
2-42 What is the Root Cause of Planar Microvoids?
2-43 Why do Planar Microvoids affect BGA Solder Joint Reliability?
2-44 Name two Industry Specifications that have information on Voids in Solder Joints
2-45 What are tin whiskers?
2-46 Can whiskers form in a vacuum?
2-47 True or False: Whiskers require a electrical current to form between two leads at different electrical potentials?
2-48 What is the most popular theory for the formation of whiskers?
2-49 What thermal treatment to the component is recommended to mitigate the risk of forming whiskers on matte tin plated parts?
2-50 What is tin pest?
Section 3
3-1 Do the land patterns for lead free need to be different than they are for tin lead?
3-2 While designing pads sizes and spacing, should one be concerned a ) more or b) less for bridging?
3-3 What is the peak reflow temperature the lead free packages must withstand?
3-4 Does the Peak Reflow Temperature requirement for lead free packages change with thickness and/pr volume of package?
3-5 How the Peak Reflow Temperature requirement for lead free packages compare with the Tin-lead packages?
3-6 How many categories are there for Part marking for lead free by JEDEC?
3-7 List some lead free surface finishes for component leads.
3-8 Why is through hole via integrity a big concern for lead free boards?
3-9 What are the ways in which the through hole via integrity can be enhanced for lead free board laminates?
3-10 What is the name of the test procedure to measure via integrity of laminates and how does it differ from temperature cycling?
3-11 True or False: Laminates that have a higher CTE above Tg are more reliable for lead free soldering than laminates with a lower CTE below Tg.
3-12 True or False: High Tg always means high reliability
3-13 Name two laminate materials that are beneficial for use in thick (>62 mils) boards.
3-14 Name of the IPC spec that provides lead free laminate requirements
3-15 What are the disadvantages of OSP surface finish over Immersion Silver surface finish for lead free boards?
3-16 Name at least five potential lead free surface finishes.
3-17 What is `Black Pad` and what is its main cause?
3-18 Which surface finish is preferred for preventing BGA Ball drop?
3-19 True or False: For 62 mils thick boards, the standard FR4 laminate is suitable for both the benign and aggressive environments on use.
3-20 List tests laminate properties that should be validated either from data sheet and from tests before using on products.
Section 4
4-1 Why are smaller metal powder diameter particles more of a concern with lead-free than tin-lead?
4-2 What is the difference between first generation, second generation and third generation solder pastes?
4-3 What printing parameters are affected due to the change over to lead free solder paste?
4-4 Does lead paste require a polished squeegee?
4-5 What are the pros and cons of keeping a 1:1 ratio between the stencil aperture and the pad for lead free?
4-6 Is the use of nitrogen atmosphere necessary during reflow soldering of lead free boards?
4-7 In the reflow soldering profile, is a soak zone always bad?
4-8 What is the impact of excessive soak in the reflow profile?
4-9 What is the effect of low peak reflow temperatures (<224C) on Lead Free BGA soldering?
4-10 Why is nitrogen blanket generally used for lead free than for tin-lead for wave solder? Is use of nitrogen essential?
4-11 True or False: Fresh solder needs to be added more frequently for LF wave solder than Tin-lead.
4-12 Why do the Copper-Tin Intermetallic Compounds in the Wave Solder Pot sink to the bottom for Sn-Cu and SnAgCu solders but float to the top for eutectic Tin-Lead solders?
4-13 What is copper dissolution or erosion? Which process is the main culprit for this phenomenon?
4-14 Is there a solder composition that prevents copper erosion?
4-15 Why is a surface treatment of standard stainless steel wave pots necessary for SAC solders?
4-16 True or False: The solder pot cleaning frequency within the maintenance cycle would be decreased for lead for lead free wave soldering. Why?
4-17 What will happen if a nitrogen atmosphere is not used during reflow for boards that contain through hole and surface mount components?
4-18 What causes fillet lifting during wave soldering?
4-19 Which selective soldering technology allows a quick change from one composition to another and does not heat the board?
4-20 What is the minimum inter-package spacing to prevent reflow of adjacent components during rework?
4-21 How do you prevent reflow of adjacent components during rework for lead-free solders?
4-22 How do you prevent unintentional mixing of lead and lead-free components during the transition phase to lead-free?
4-23 True or False: The width of the process window for reflow and rework a lead-free BGA is the same as that for reworking a tin-lead BGA.
4-24 Are lead free materials being identified in a different than tin-lead to help differentiate them at incoming and avoid unintentional mixing?
4-25 True or False: ICT Probes do not require any modifications for Lead-free Boards
Section 5
5-1 What is the main concern during the transition phase to lead free?
5-2 Define Forward Compatibility in the context of Lead Free Soldering.
5-3 Define Backward Compatibility in the context of Lead Free Soldering.
5-4 Why do Forward Compatibility Solder Joints contain more trapped voids than Lead free solder joints?
5-5 Why are Backward Compatibility BGA Solder Joints inhomogeneous in composition?
5-6 True or False: Backward Compatibility BGA solder joints self align if the peak reflow solder temperature is less than the melting temperature if the BGA solder balls?
5-7 What can be done during the reflow soldering process to enhance the reliability of Backward Compatibility Solder joints?
5-8 What scenario results in Forward Compatibility Solder Joints on Lead-free boards?
5-9 What scenario results in Backward Compatibility Solder Joints on Tin-lead boards?
5-10 What are the concerns in using a compromise profile in backward and forward compatibility scenarios?
5-11 Is there a soldering solution available to prevent the use of compromise profile in backward or forward compatibility issues
5-12 True or False: Compliance and enforcement falls within the jurisdiction of each EU Member State?
5-13 Who and how the RoHS compliance will be enforced?
5-14 What is verifiable objective evidence as it relates to RoHS compliance?
5-15 Is self-declaration an acceptable basis for RoHS compliance?
5-16 In which country self-declaration may not be acceptable for RoHS compliance?
5-17 True or False: EU member states have clearly defined what paperwork is necessary to prove RoHS compliance?
5-18 How long should you keep RoHS compliance information?
5-19 What is a material declaration and what is it used for?
5-20 What is the number of IPC material declaration standard? What are the key items it asks to be declared?
5-21 How many material declaration classes are specified in IPC 1752?
5-22 What is the JIG List and how many substances does it contain?
5-23 What is the difference between Jig A and Jig B list?
5-24 What is a Chemical Abstract Service (CAS) registry number?
5-25 True or false: suppliers must create new part numbers for RoHS compliant parts?
5-26 True or False: As far as the consumer is concerned, compliance to WEEE is voluntary
5-27 What is the difference between RoHS 6/6, 0/6 and RoHS 5/6?
5-28 How do you know whether you are 5/6 or 6/6 RoHS compliant?
5-29 As it relates to component, process, bare board perspective, when can you claim a 6/6 compliance?
5-30 What are the potential areas you need to be watchful when you offer compliance certificates..
5-31 True or False: China RoHS restricts the same substances as EU RoHS?
5-32 True or false: RoHS 6/6 means the green “e” China RoHS label can be used?
5-33 True or false: China RoHS requires product testing for compliance?
5-34 What are the pros and cons of implementing lead-free in-house or going to a EMS Assembly house?
5-35 What are some of the key questions that you should ask when selecting a lead free supplier?
Section 1
1-1 What is the definition of Lead Free?
1-2 How many categories of Lead free Readiness are there? Name Them
1-3 In the US, which material is recycled more: Batteries, newspapers, aluminum cans, glass bottles.
1-4 True or False: RoHS is the legislation for elimination of lead only.
1-5 When was the effective date for the RoHS legislation.
1-6 What does WEEE stand for and what does it control? When did it become effective?
1-7 List the names of some materials that are exempt from RoHS.
1-8 What would be the most significant item that will limit your ability to convert products to lead free, despite your company's full commitment of resources and people?
1-9 True or False: One can currently buy lead free products on the market today. Are they totally lead free?
1-10 Which is the main driver for lead free products today: Legislation or Competitive Pressure.
1-11 True or False: When did China RoHS become effective?. Is RoHS directive by China is less or more restrictive than EU?
1-12 True of False: In USA there is no legal requirement for RoHS compliance
1-13 List the names of some Industry Consortias working towards lead-free implementation.
1-14 List the new capital equipment that you will need for lead free conversion.
1-17 True or False: Lead Metal is cheaper than Tin Metal
1-18 What are the benefits of maintaining dual manufacturing lines, i.e., Lead-free and Tin-Lead?
1-19 What does the WEEE man represent?
1-20 Which category is the largest when doing the calculations for the WEEE man
1-21 Describe the Symbol for Marking of EEE for Separate Collection?
1-22 How much mercury is allowed in EU directive?
1-18 True or False: California has passed the RoHS directive as EU. When did it effective?
Section 2
2-1 What are the key requirements for selecting a lead free solder?
2-2 What is the definition of a eutectic composition?
2-3 Give some examples if binary solder systems which exhibit eutectic behavior.
2-4 How do you find a eutectic composition on a binary phase diagram?
2-5 What are the advantages of Bismuth containing solders?
2-6 What are the disadvantages of Bismuth Containing solders?
2-7 Why are indium containing solders not preferred as the best choice for lead free solders?
2-8 Tin-zinc eutectic solders have a lower melting point as well as better mechanical properties than SAC solders. Yet, tin-zinc solders are not preferred to SAC solders. Why?
2-9 Besides the high cost of gold, why are gold containing solders not considered for use in lead free soldering?
2-10 What are the compositions of the most popular lead free solder alloys chosen around the world?
2-11 What is the composition of SAC396 alloy?
2-12 Why is the SAC305 composition preferred over SAC405?
2-13 True or False: SAC solders melt completely at a lower temperature than eutectic Sn-Pb solder.
2-14 What is the typical Peak reflow Temperature during the lead free soldering process?
2-15 What are some of the material properties considered when choosing potential lead free solders by the Industry consortia that initially worked on the selection process?
2-16 What is the typical microstructure of the SAC305 alloy?
2-17 What is the typical microstructure of SAC405 alloy and why is it dependant on the cooling rate of the solder joints as they exit the reflow soldering oven?
2-18 True or False: Lead free soldering results in thicker Intermetallic Compounds at the solder to copper land interfaces?
2-19 What are the intermetallic compound compositions that form when SAC solder is reflowed on an OSP coated copper land?
2-20 What are the Intermetallic compounds that form when SAC solder is reflow soldered on an Immersion Silver coated copper land?
2-21 What is the composition of the SN100C Wave Solder lead free alloy and what does it’s manufacturer claim are its advantages over other lead free wave solder alloys?
2-22 Besides SN100C, what are the other wave solder alloys being marketed today? List some advantageous properties of these alloys.
2-23 What is the range of wetting angle that is considered an indication of an excellent quality solder joint?
2-24 True or False: SAC solders have lower wetting angle than eutectic SnPb solders.
2-25 Ture or False: SAC solders typically have a dull look when inspected visually as compared to eutectic SnPb solders.
2-26 True or False: Under low strain conditions, SAC solders are better than SnPb solders when subjected to temperature cycling tests.
2-27 What is the observed damaged mechanism within the microstructure of a SAC BGA solder joint and how does it differ from that of a eutectic SnPb solder joint?
2-28 True or False: For rigid packages such as LCCCs, CBGAs, Resistors, TSOPs, Flip Chips, SnPb solder is better than SAC
2-29 Why has mechanical shock and drop resistance of solders become an important aspect of product reliability recently?
2-30 Why are SAC solders significantly worse than eutectic SnPb solders during mechanical shock and drop tests?
2-31 Why is SAC105 composition better than SAC305 for mechanical shock and drop resistance? What are the disadvantaged of SAC105 with respect to the SAC305 and SAC405 compositions?
2-32 What is Pad Cratering and when does it occur?
2-33 Why is Pad Cratering more prevalent when SAC solders are used than when SnPb solders are used?
2-34 What are some ways of mitigating Pad Cratering?
2-35 What is the difference between Planar MicroVoids and Micro Via Voids?
2-36 True or False: Shrink hole voids are present in solder joints irrespective of the solder composition
2-37 Is there a consensus on the testing protocol (ramp rate and dwell times at temperature extremes) for thermal cycling of lead free board products?
2-38 Does a longer dwell time at the temperature extremes during thermal cycling, enhance or diminish SAC alloy solder joint life?.
2-39 True or False: Wetting time increases with Increasing Temperature for Lead Free Alloys
2-40 True or False: IMC Microvoids can be minimized by optimizing the reflow soldering profile
2-41 Describe Macrovoids. How do they differ from Planar Microvoids.
2-42 What is the Root Cause of Planar Microvoids?
2-43 Why do Planar Microvoids affect BGA Solder Joint Reliability?
2-44 Name two Industry Specifications that have information on Voids in Solder Joints
2-45 What are tin whiskers?
2-46 Can whiskers form in a vacuum?
2-47 True or False: Whiskers require a electrical current to form between two leads at different electrical potentials?
2-48 What is the most popular theory for the formation of whiskers?
2-49 What thermal treatment to the component is recommended to mitigate the risk of forming whiskers on matte tin plated parts?
2-50 What is tin pest?
Section 3
3-1 Do the land patterns for lead free need to be different than they are for tin lead?
3-2 While designing pads sizes and spacing, should one be concerned a ) more or b) less for bridging?
3-3 What is the peak reflow temperature the lead free packages must withstand?
3-4 Does the Peak Reflow Temperature requirement for lead free packages change with thickness and/pr volume of package?
3-5 How the Peak Reflow Temperature requirement for lead free packages compare with the Tin-lead packages?
3-6 How many categories are there for Part marking for lead free by JEDEC?
3-7 List some lead free surface finishes for component leads.
3-8 Why is through hole via integrity a big concern for lead free boards?
3-9 What are the ways in which the through hole via integrity can be enhanced for lead free board laminates?
3-10 What is the name of the test procedure to measure via integrity of laminates and how does it differ from temperature cycling?
3-11 True or False: Laminates that have a higher CTE above Tg are more reliable for lead free soldering than laminates with a lower CTE below Tg.
3-12 True or False: High Tg always means high reliability
3-13 Name two laminate materials that are beneficial for use in thick (>62 mils) boards.
3-14 Name of the IPC spec that provides lead free laminate requirements
3-15 What are the disadvantages of OSP surface finish over Immersion Silver surface finish for lead free boards?
3-16 Name at least five potential lead free surface finishes.
3-17 What is `Black Pad` and what is its main cause?
3-18 Which surface finish is preferred for preventing BGA Ball drop?
3-19 True or False: For 62 mils thick boards, the standard FR4 laminate is suitable for both the benign and aggressive environments on use.
3-20 List tests laminate properties that should be validated either from data sheet and from tests before using on products.
Section 4
4-1 Why are smaller metal powder diameter particles more of a concern with lead-free than tin-lead?
4-2 What is the difference between first generation, second generation and third generation solder pastes?
4-3 What printing parameters are affected due to the change over to lead free solder paste?
4-4 Does lead paste require a polished squeegee?
4-5 What are the pros and cons of keeping a 1:1 ratio between the stencil aperture and the pad for lead free?
4-6 Is the use of nitrogen atmosphere necessary during reflow soldering of lead free boards?
4-7 In the reflow soldering profile, is a soak zone always bad?
4-8 What is the impact of excessive soak in the reflow profile?
4-9 What is the effect of low peak reflow temperatures (<224C) on Lead Free BGA soldering?
4-10 Why is nitrogen blanket generally used for lead free than for tin-lead for wave solder? Is use of nitrogen essential?
4-11 True or False: Fresh solder needs to be added more frequently for LF wave solder than Tin-lead.
4-12 Why do the Copper-Tin Intermetallic Compounds in the Wave Solder Pot sink to the bottom for Sn-Cu and SnAgCu solders but float to the top for eutectic Tin-Lead solders?
4-13 What is copper dissolution or erosion? Which process is the main culprit for this phenomenon?
4-14 Is there a solder composition that prevents copper erosion?
4-15 Why is a surface treatment of standard stainless steel wave pots necessary for SAC solders?
4-16 True or False: The solder pot cleaning frequency within the maintenance cycle would be decreased for lead for lead free wave soldering. Why?
4-17 What will happen if a nitrogen atmosphere is not used during reflow for boards that contain through hole and surface mount components?
4-18 What causes fillet lifting during wave soldering?
4-19 Which selective soldering technology allows a quick change from one composition to another and does not heat the board?
4-20 What is the minimum inter-package spacing to prevent reflow of adjacent components during rework?
4-21 How do you prevent reflow of adjacent components during rework for lead-free solders?
4-22 How do you prevent unintentional mixing of lead and lead-free components during the transition phase to lead-free?
4-23 True or False: The width of the process window for reflow and rework a lead-free BGA is the same as that for reworking a tin-lead BGA.
4-24 Are lead free materials being identified in a different than tin-lead to help differentiate them at incoming and avoid unintentional mixing?
4-25 True or False: ICT Probes do not require any modifications for Lead-free Boards
Section 5
5-1 What is the main concern during the transition phase to lead free?
5-2 Define Forward Compatibility in the context of Lead Free Soldering.
5-3 Define Backward Compatibility in the context of Lead Free Soldering.
5-4 Why do Forward Compatibility Solder Joints contain more trapped voids than Lead free solder joints?
5-5 Why are Backward Compatibility BGA Solder Joints inhomogeneous in composition?
5-6 True or False: Backward Compatibility BGA solder joints self align if the peak reflow solder temperature is less than the melting temperature if the BGA solder balls?
5-7 What can be done during the reflow soldering process to enhance the reliability of Backward Compatibility Solder joints?
5-8 What scenario results in Forward Compatibility Solder Joints on Lead-free boards?
5-9 What scenario results in Backward Compatibility Solder Joints on Tin-lead boards?
5-10 What are the concerns in using a compromise profile in backward and forward compatibility scenarios?
5-11 Is there a soldering solution available to prevent the use of compromise profile in backward or forward compatibility issues
5-12 True or False: Compliance and enforcement falls within the jurisdiction of each EU Member State?
5-13 Who and how the RoHS compliance will be enforced?
5-14 What is verifiable objective evidence as it relates to RoHS compliance?
5-15 Is self-declaration an acceptable basis for RoHS compliance?
5-16 In which country self-declaration may not be acceptable for RoHS compliance?
5-17 True or False: EU member states have clearly defined what paperwork is necessary to prove RoHS compliance?
5-18 How long should you keep RoHS compliance information?
5-19 What is a material declaration and what is it used for?
5-20 What is the number of IPC material declaration standard? What are the key items it asks to be declared?
5-21 How many material declaration classes are specified in IPC 1752?
5-22 What is the JIG List and how many substances does it contain?
5-23 What is the difference between Jig A and Jig B list?
5-24 What is a Chemical Abstract Service (CAS) registry number?
5-25 True or false: suppliers must create new part numbers for RoHS compliant parts?
5-26 True or False: As far as the consumer is concerned, compliance to WEEE is voluntary
5-27 What is the difference between RoHS 6/6, 0/6 and RoHS 5/6?
5-28 How do you know whether you are 5/6 or 6/6 RoHS compliant?
5-29 As it relates to component, process, bare board perspective, when can you claim a 6/6 compliance?
5-30 What are the potential areas you need to be watchful when you offer compliance certificates..
5-31 True or False: China RoHS restricts the same substances as EU RoHS?
5-32 True or false: RoHS 6/6 means the green “e” China RoHS label can be used?
5-33 True or false: China RoHS requires product testing for compliance?
5-34 What are the pros and cons of implementing lead-free in-house or going to a EMS Assembly house?
5-35 What are some of the key questions that you should ask when selecting a lead free supplier?
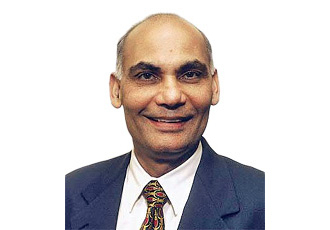
Registration is Open for SMT Course
Ray Prasad will be teaching his flagship SMT course: