SMT - Lead-free Reflow Profile Development : Part 2
As discussed in my February column, to accommodate constraints imposed by large components with high thermal mass requiring higher peak
temperature for longer durations, a tighter process control is required to achieve good soldering results in lead-free assemblies. The same is true for smaller, temperature sensitive components requiring lower peak temperatures for shorter durations. Backward- compatibility issues in which some lead-free components must be used on a primarily tin/lead board can compound the problem further.
Let’s look at backward compatibility, in which some components are only available with lead-free surface finishes. It is not economical for component suppliers to supply both tin/lead and lead-free versions of the same component. There is no issue when using leaded components with lead-free surface finishes. The real problem arises when using lead-free BGAs on a primarily tin/lead board. If the tin/lead profile with maximum peak temperature of 220˚C is used because all components are tin/lead, BGA balls will reflow partially, or not at all, creating a serious solder joint reliability issue. What kind of reflow profile should be used? There are two options:
Option 1. Use the standard tin/lead reflow profile with peak reflow of 210˚ to 220˚C for all components except lead-free BGAs. Do not place lead-free BGAs with other tin/lead components. After tin/lead components have been reflow-soldered, use selective soldering with a laser to place and solder all lead-free BGAs. The selective laser soldering system will place and solder only lead-free BGAs without impacting neighboring tin/lead components already soldered in the convection oven. If you do not have access to a laser selective soldering system, use option 2.
Option 2. If you want to solder all tin/ lead components and some lead-free BGAs in the same oven because tin/lead versions
are unavailable, you must use a peak temperature that will not damage the tin/lead components, but is sufficient enough to reflow lead-free BGAs. Keep in mind that you will use tin/lead solder paste because most of the components on the board are tin/lead. Therefore, a peak temperature of 210˚ to 220˚C will be suitable for tin/lead, but inadequate for lead-free BGA balls with melting point of 217˚ to 221˚C. A peak temperature of 226˚ to 228˚C with 45 to 60 seconds time above liquidus (TAL) will be sufficient to reflow lead-free BGAs without damaging all tin/lead components on the same board.
If the tight reflow temperature band of 226˚ to 228˚C is difficult to achieve to solder
both tin/lead and lead-free BGAs in a backward- compatible scenario, consider selective laser soldering, or find an alternative source for BGAs with tin/lead balls. When developing any profile, it is important to use the right thermocouple. Type-k thermocouples with a wire gauge of 36 AWG should be used. Thicker thermocouple wires add too much heat sink. Never use high-temperature tapes, such as polyimide (kapton) or aluminum tapes, because they tend to come loose during reflow; and you may measure the temperature of the air in the oven, not the temperature of the solder joints. Always use high-temperature solder or thermally conductive adhesive to attach thermocouples to the solder joints.
In the case of BGAs, drill holes in the inner and outer rows of BGA pads from the bottom of the board, and push the thermocouples almost to the top surface to measure the temperature of BGA balls. BGA ball temperatures of inner and outer rows must be within 2˚C of each other. Four to six thermocouples should be attached at various component locations to represent the lowest to highest thermal-mass areas, including at least two thermocouples for BGAs.
Unique Profile for Each Product
There is some misunderstanding that one convection oven profile will work for all boards, and there is no need to develop a unique profile for each board. This is not true because each board has a different thermal mass, and one may have different loading patterns. The same double-sided board, depending on component placement and distribution of copper planes on each side, may require different profiles for each side. There also is a misconception that if you must change a profile, you can change the belt speed. Changing only the belt speed is easy, but it may not be the right approach because it changes the temperature of the board in every zone. Commercial hardware and software packages are available to ease thermal-profile development.
Once the desired profile is achieved, run a production board with solder paste and components for reflow. After reflow, inspect the solder joint quality. A random problem in only a specific section of the board may be related to solderability; a consistent problem in a given section may be related to the solder profile due to nonuniform heating. Consistent problems may also be related to paste quality and landpattern design.
Once the profile gives the desired results (assuming design and other material variables have been optimized), document the profile. After this point, no changes should be allowed in the profile.
SMT - Lead-free Reflow Profile Development: Part 1
temperature for longer durations, a tighter process control is required to achieve good soldering results in lead-free assemblies. The same is true for smaller, temperature sensitive components requiring lower peak temperatures for shorter durations. Backward- compatibility issues in which some lead-free components must be used on a primarily tin/lead board can compound the problem further.
Let’s look at backward compatibility, in which some components are only available with lead-free surface finishes. It is not economical for component suppliers to supply both tin/lead and lead-free versions of the same component. There is no issue when using leaded components with lead-free surface finishes. The real problem arises when using lead-free BGAs on a primarily tin/lead board. If the tin/lead profile with maximum peak temperature of 220˚C is used because all components are tin/lead, BGA balls will reflow partially, or not at all, creating a serious solder joint reliability issue. What kind of reflow profile should be used? There are two options:
Option 1. Use the standard tin/lead reflow profile with peak reflow of 210˚ to 220˚C for all components except lead-free BGAs. Do not place lead-free BGAs with other tin/lead components. After tin/lead components have been reflow-soldered, use selective soldering with a laser to place and solder all lead-free BGAs. The selective laser soldering system will place and solder only lead-free BGAs without impacting neighboring tin/lead components already soldered in the convection oven. If you do not have access to a laser selective soldering system, use option 2.
Option 2. If you want to solder all tin/ lead components and some lead-free BGAs in the same oven because tin/lead versions
are unavailable, you must use a peak temperature that will not damage the tin/lead components, but is sufficient enough to reflow lead-free BGAs. Keep in mind that you will use tin/lead solder paste because most of the components on the board are tin/lead. Therefore, a peak temperature of 210˚ to 220˚C will be suitable for tin/lead, but inadequate for lead-free BGA balls with melting point of 217˚ to 221˚C. A peak temperature of 226˚ to 228˚C with 45 to 60 seconds time above liquidus (TAL) will be sufficient to reflow lead-free BGAs without damaging all tin/lead components on the same board.
If the tight reflow temperature band of 226˚ to 228˚C is difficult to achieve to solder
both tin/lead and lead-free BGAs in a backward- compatible scenario, consider selective laser soldering, or find an alternative source for BGAs with tin/lead balls. When developing any profile, it is important to use the right thermocouple. Type-k thermocouples with a wire gauge of 36 AWG should be used. Thicker thermocouple wires add too much heat sink. Never use high-temperature tapes, such as polyimide (kapton) or aluminum tapes, because they tend to come loose during reflow; and you may measure the temperature of the air in the oven, not the temperature of the solder joints. Always use high-temperature solder or thermally conductive adhesive to attach thermocouples to the solder joints.
In the case of BGAs, drill holes in the inner and outer rows of BGA pads from the bottom of the board, and push the thermocouples almost to the top surface to measure the temperature of BGA balls. BGA ball temperatures of inner and outer rows must be within 2˚C of each other. Four to six thermocouples should be attached at various component locations to represent the lowest to highest thermal-mass areas, including at least two thermocouples for BGAs.
Unique Profile for Each Product
There is some misunderstanding that one convection oven profile will work for all boards, and there is no need to develop a unique profile for each board. This is not true because each board has a different thermal mass, and one may have different loading patterns. The same double-sided board, depending on component placement and distribution of copper planes on each side, may require different profiles for each side. There also is a misconception that if you must change a profile, you can change the belt speed. Changing only the belt speed is easy, but it may not be the right approach because it changes the temperature of the board in every zone. Commercial hardware and software packages are available to ease thermal-profile development.
Once the desired profile is achieved, run a production board with solder paste and components for reflow. After reflow, inspect the solder joint quality. A random problem in only a specific section of the board may be related to solderability; a consistent problem in a given section may be related to the solder profile due to nonuniform heating. Consistent problems may also be related to paste quality and landpattern design.
Once the profile gives the desired results (assuming design and other material variables have been optimized), document the profile. After this point, no changes should be allowed in the profile.
SMT - Lead-free Reflow Profile Development: Part 1
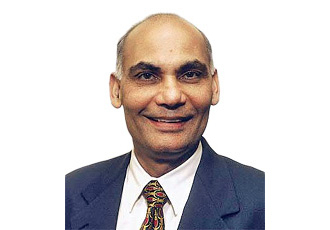
Registration is Open for SMT Course
Ray Prasad will be teaching his flagship SMT course: