Selective Automated Laser Assembly of SMT Assemblies
Let me first take this rare, rather once in a lifetime, opportunity to wish all of you, the readers of this column, a Happy New Millenium, the start of the 21st century. This also is the time for many of you to think about Sunny San Diego. I am not talking about the boardwalk and the sandy beaches, although they are certainly very pleasant, but APEX, the premier trade show of our industry. Last year’s APEX show in Long Beach was a resounding success by any measure even though it was its first year. The early indications are that it will be an even better trade show this year.
People come to trade shows for many reasons ¾ to attend professional tutorials and workshops, to participate in technical sessions, and to see the latest in assembly technology and equipment. Numerous suppliers will introduce new equipment in paste printing, pick-and-place, reflow soldering, inspection, and rework. In this column, I will preview a laser assembly machine (not just a laser soldering machine) made by BeamWorks that performs all assembly functions (no, it does not make coffee).
Before I describe this machine, let me make a public disclosure to avoid any conflict of interest. I have consulted for BeamWorks since the company’s inception about three years ago and now have significant involvement in the company’s operation. Rest assured, however, that as in my past columns, I will give a balanced technical opinion whether I am working with a given company or not.
Addressing Concerns
This system is attempting to address some key technical concerns in our industry. The first concern is selective assembly of through-hole components such as sockets and connectors. These problems will not dissipate because through-hole components will remain in the SMT industry for many years. There are many reasons for this, but that is content for another column.
In a mixed assembly, through-hole components are soldered selectively by three methods:
• Wave soldering using a specially designed fixture
• Paste-in-hole process
• Hand soldering.
When selective wave soldering and paste-in-hole process are not technically feasible, as typically is the case, hand soldering is used as the “last resort” process. Hand soldering is not only slow and expensive, but also operator-dependent, resulting in inconsistent solder joint quality. Additionally, hand soldered joints are susceptible to external and internal damage. The internal damage is a serious concern because the solder joint appears fine on the board’s surface but would be highly unreliable even if it passed electrical tests.
Through-hole components are not the only drivers for selective soldering. With increased cell phone use, selective RF shield soldering is becoming very common. While some RF shields can be reflow soldered in convection ovens, many still need to be soldered by hand. Even shields that can be soldered in convection ovens require hand soldering for removal to allow rework of components shielded by them. Additionally, there are many surface mount connectors, especially those with leads on each side of the board, that need to be selectively soldered.
Furthermore, moisture-sensitive devices must be baked before soldering to prevent package cracking, commonly referred to as popcorning. Reworking an expensive device that must be salvaged is especially painful. To salvage an individual component, the entire assembly must be baked for 24 hours to seven days. The potential for localized board damage is increased greatly when removing large components such as fine pitch, plastic leaded chip carriers (PLCC), ball grid arrays (BGA) and small components such as chip scale packages (CSP). This problem will get worse before it gets better when (and if) lead-free solders must be used because most have very high melting points.
Laser Assembly Machine
The key concerns in today’s electronics assembly are selective assembly of through-hole components, missing and moisture-sensitive surface mount components, and lead-free soldering, and soldering of RF shields. The BeamWorks laser assembly machine’s ability to selectively assemble any component addresses these technical concerns. It not only is a laser soldering machine but also an assembly machine, performing all the assembly functions from paste dispensing to inspection and rework. This machine dispenses solder paste with positive force displacement to accurately control paste volume. Then various pick-up heads pick up components from as small as 0402 to as large as BGAs and fine pitch. Multiple diode lasers selectively or simultaneously solder in milliseconds. Because laser cannot see BGA, CSP and flip chip balls, the laser beam width is increased to simulate an oven profile to reflow hidden solder balls. The system also can perform rework and inspection functions. The need for programming is eliminated because computer-aided design (CAD) data is used for all assembly functions ¾ paste dispensing, placement, soldering and rework. Components such as fine pitch do not have to be baked because the package does not get hot, only the leads do.
The machine can be used for both high-volume and low-volume applications. For example, if it is used only as a soldering machine (and I do not see why it should be), multiple lasers can keep up with the high-volume pick-and-place machine in the line. Also, it can be used to selectively assemble components in a high-volume line. Examples include missing components in an already assembled board or an RF shield in a high-volume line. In low-volume applications, it can assemble all components in quick-turn applications. If the machine is used for every assembly processes; however, it naturally will be slower. In prototype and pilot builds, volume is not a concern, but quick turn around time is.
While this machine can be used for low-volume, quick-turn applications, it is well suited for unique applications where conventional processes either are not technically feasible or are too expensive. Additionally, because reflow time for each joint can be individually programmed, the heat input for each joint can be precisely tailored to meet the needs of joints connected to power and ground planes or heat sinks.
Because this machine measures soldering time in milliseconds (as opposed to seconds), the intermetallic thickness is under 1 mm (or less than 40 m". Compare this to 500 m" or more in other soldering methods), greatly improving solder joint reliability.
This machine is not a panacea for all our ills ¾ but nothing is. It does, however, meet some unique needs and, while it cannot be used to replace existing equipment, it can be used as a supplement.
Those who would like to see the machine in operation can do so at APEX 2001 where it will be unveiled to the world for the first time.
Hope to see you in sunny San Diego!
SMT
RAY P. PRASAD is an SMT Editorial Advisory Board member and author of the textbook Surface Mount Technology: Principles and Practice. Additionally, he is president of BeamWorks Inc. in Portland, OR and founder of the Ray Prasad Consultancy Group, which specializes in helping companies establish strong internal SMT infrastructure. Contact him at www.rayprasad.com.
People come to trade shows for many reasons ¾ to attend professional tutorials and workshops, to participate in technical sessions, and to see the latest in assembly technology and equipment. Numerous suppliers will introduce new equipment in paste printing, pick-and-place, reflow soldering, inspection, and rework. In this column, I will preview a laser assembly machine (not just a laser soldering machine) made by BeamWorks that performs all assembly functions (no, it does not make coffee).
Before I describe this machine, let me make a public disclosure to avoid any conflict of interest. I have consulted for BeamWorks since the company’s inception about three years ago and now have significant involvement in the company’s operation. Rest assured, however, that as in my past columns, I will give a balanced technical opinion whether I am working with a given company or not.
Addressing Concerns
This system is attempting to address some key technical concerns in our industry. The first concern is selective assembly of through-hole components such as sockets and connectors. These problems will not dissipate because through-hole components will remain in the SMT industry for many years. There are many reasons for this, but that is content for another column.
In a mixed assembly, through-hole components are soldered selectively by three methods:
• Wave soldering using a specially designed fixture
• Paste-in-hole process
• Hand soldering.
When selective wave soldering and paste-in-hole process are not technically feasible, as typically is the case, hand soldering is used as the “last resort” process. Hand soldering is not only slow and expensive, but also operator-dependent, resulting in inconsistent solder joint quality. Additionally, hand soldered joints are susceptible to external and internal damage. The internal damage is a serious concern because the solder joint appears fine on the board’s surface but would be highly unreliable even if it passed electrical tests.
Through-hole components are not the only drivers for selective soldering. With increased cell phone use, selective RF shield soldering is becoming very common. While some RF shields can be reflow soldered in convection ovens, many still need to be soldered by hand. Even shields that can be soldered in convection ovens require hand soldering for removal to allow rework of components shielded by them. Additionally, there are many surface mount connectors, especially those with leads on each side of the board, that need to be selectively soldered.
Furthermore, moisture-sensitive devices must be baked before soldering to prevent package cracking, commonly referred to as popcorning. Reworking an expensive device that must be salvaged is especially painful. To salvage an individual component, the entire assembly must be baked for 24 hours to seven days. The potential for localized board damage is increased greatly when removing large components such as fine pitch, plastic leaded chip carriers (PLCC), ball grid arrays (BGA) and small components such as chip scale packages (CSP). This problem will get worse before it gets better when (and if) lead-free solders must be used because most have very high melting points.
Laser Assembly Machine
The key concerns in today’s electronics assembly are selective assembly of through-hole components, missing and moisture-sensitive surface mount components, and lead-free soldering, and soldering of RF shields. The BeamWorks laser assembly machine’s ability to selectively assemble any component addresses these technical concerns. It not only is a laser soldering machine but also an assembly machine, performing all the assembly functions from paste dispensing to inspection and rework. This machine dispenses solder paste with positive force displacement to accurately control paste volume. Then various pick-up heads pick up components from as small as 0402 to as large as BGAs and fine pitch. Multiple diode lasers selectively or simultaneously solder in milliseconds. Because laser cannot see BGA, CSP and flip chip balls, the laser beam width is increased to simulate an oven profile to reflow hidden solder balls. The system also can perform rework and inspection functions. The need for programming is eliminated because computer-aided design (CAD) data is used for all assembly functions ¾ paste dispensing, placement, soldering and rework. Components such as fine pitch do not have to be baked because the package does not get hot, only the leads do.
The machine can be used for both high-volume and low-volume applications. For example, if it is used only as a soldering machine (and I do not see why it should be), multiple lasers can keep up with the high-volume pick-and-place machine in the line. Also, it can be used to selectively assemble components in a high-volume line. Examples include missing components in an already assembled board or an RF shield in a high-volume line. In low-volume applications, it can assemble all components in quick-turn applications. If the machine is used for every assembly processes; however, it naturally will be slower. In prototype and pilot builds, volume is not a concern, but quick turn around time is.
While this machine can be used for low-volume, quick-turn applications, it is well suited for unique applications where conventional processes either are not technically feasible or are too expensive. Additionally, because reflow time for each joint can be individually programmed, the heat input for each joint can be precisely tailored to meet the needs of joints connected to power and ground planes or heat sinks.
Because this machine measures soldering time in milliseconds (as opposed to seconds), the intermetallic thickness is under 1 mm (or less than 40 m". Compare this to 500 m" or more in other soldering methods), greatly improving solder joint reliability.
This machine is not a panacea for all our ills ¾ but nothing is. It does, however, meet some unique needs and, while it cannot be used to replace existing equipment, it can be used as a supplement.
Those who would like to see the machine in operation can do so at APEX 2001 where it will be unveiled to the world for the first time.
Hope to see you in sunny San Diego!
SMT
RAY P. PRASAD is an SMT Editorial Advisory Board member and author of the textbook Surface Mount Technology: Principles and Practice. Additionally, he is president of BeamWorks Inc. in Portland, OR and founder of the Ray Prasad Consultancy Group, which specializes in helping companies establish strong internal SMT infrastructure. Contact him at www.rayprasad.com.
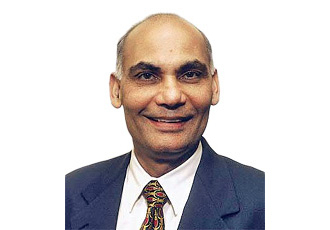
Registration is Open for SMT Course
Ray Prasad will be teaching his flagship SMT course: