Selective Laser Soldering: DfM Rules
All soldering processes have specific design for manufacturing (DfM) requirements. For example, via-in-pad is not desired in reflow to prevent insufficient solder, and the right gap between pads of chip components is necessary to prevent tombstoning. For wave soldering of surface mount components glued to the bottom of the board, it is necessary to align them parallel to the wave to prevent solder skips.
In selective wave soldering of thru-hole components when surface mount components are reflow soldered on both top and bottom sides, adequate space between surface mount and thru-hole components is necessary. This space allows the wave fixture to hide surface mount components from the wave while selectively soldering thru-hole components.
Similarly, when thru-hole components are soldered using paste-in-hole processing, additional spacing around the thru-hole component is necessary to allow desired volume of solder paste around the thru-hole pads to achieve 100% solder fillets. In addition, it is important to allow the right gap between the lead and the hole. For example, the plated thru-hole (PTH) diameter should be about 12 mils larger than the lead diameter to allow capillary action to fill solder in the PTH. If the gap is too large, paste-in-hole processing may not provide acceptable solder fillets.
Technology options are coming on-line for selectively soldering thru-hole components in a mixed assembly. Laser soldering is one example. In my discussion of laser, I fully disclose that I am associated with laser soldering company BeamWorks. As there also are other valuable suppliers of laser soldering equipment, I am talking about laser systems in general in this article, and not about BeamWorks in particular.
Before we get into laser soldering DfM discussion, let us briefly discuss the laser soldering process, since it is relatively new. Laser soldering uses diode lasers to heat the component lead and PTH pad while automatically feeding solder wire to achieve the desired fillet. The wire has flux inside its core. This is a point-to-point soldering process similar to hand soldering, but it is faster and produces consistent quality, a key concern in hand soldering. Another laser soldering benefit, transitions from tin/lead to lead-free take minutes, requiring only that operators replace the solder wire spool.
Some high-end laser systems have built-in infrared (IR) sensors to monitor joint temperature during soldering. This IR sensor monitors the temperature of connections being made and automatically controls the duration of soldering to prevent either cold solder or board discoloration. Soldering duration generally is around 1 sec./joint, varying with surface finish, hole-to-lead-diameter ratio, component color, board thermal mass, and other factors. IR sensors allow precise process control by treating each joint according to its thermal requirement, using closed-loop feedback. Now here is the catch.
The IR sensor is sensitive to the color of component and board surfaces and soldermasks. It requires a minimum gap between the lead and hole diameter, similar to paste-in-hole processes. It is necessary, therefore, to follow certain DfM rules with laser soldering.
PTH diameter should not be much bigger than 20% of the lead diameter. The tighter gap between the lead and hole minimizes the amount of laser hitting the bottom of the component above the board surface. The objective is to heat the lead and not the bottom of the component.
If the PTH hole diameter is too large, it's optimal to have lighter components to reflect the laser away from the component body to the component lead where it is needed most. This will encourage good solder fillets in shortest possible soldering times. As a guideline, whenever possible, use components with lighter, preferably white, color rather than components with dark or black colors. When that is not possible, it is even more critical to maintain the smallest gap between the PTH hole and lead diameter.
Laser power also is sensitive to the color of board surface finish. Gold or electroless nickel immersion gold (ENIG) finishes will reflect laser more than a duller surface - tin or hot air solder leveling (HASL); hence, the laser will stay on for a longer time. Longer soldering times may result in board discoloration.
Lasers used in selective soldering typically have 2-mm diameters. It is better to have much bigger pad (annular ring) than normal; the pad will absorb the laser heat and protect the surrounding soldermask. If this is not possible, it is necessary to allow sufficient clearance between the pad and soldermask to prevent soldermask discoloration. Again, lighter, brighter, and shinier soldermasks are better than duller soldermasks, since they reflect laser heat to prevent discoloration.
It is helpful to have the same lead-length protrusion throughout the assembly. Fortunately, long lead protrusion is more acceptable with laser than wave - 2-2.5 mm for laser as opposed to ideally 1 mm in wave for bridge and icicle prevention. Some guidelines about spacing between taller and smaller components are in order as well, if the laser goes in at an angle. The greater the spacing between taller and smaller components, the lower the potential for shadowing from taller adjacent components. If extra spacing between components is not possible, attempt should be made during layout stage to place components of similar heights as neighbors.
There should be no flux on the board surface after the reflow process is completed for surface mount components. In other words, when the surface mount components are reflow soldered prior to selective laser soldering of thru-hole components, they should be cleaned properly. Why? Flux or paste in the sight of laser beam will burn. If the board is not cleaned after reflow, as would be the case for no-clean specs, it is recommended that you use low- or no-residue solder paste. This is helpful in preventing corrosion potential in the field, especially in humid environments.
Conclusion
In selective wave soldering of thru-hole components when surface mount components are reflow soldered on both top and bottom sides, adequate space between surface mount and thru-hole components is necessary. This space allows the wave fixture to hide surface mount components from the wave while selectively soldering thru-hole components.
Similarly, when thru-hole components are soldered using paste-in-hole processing, additional spacing around the thru-hole component is necessary to allow desired volume of solder paste around the thru-hole pads to achieve 100% solder fillets. In addition, it is important to allow the right gap between the lead and the hole. For example, the plated thru-hole (PTH) diameter should be about 12 mils larger than the lead diameter to allow capillary action to fill solder in the PTH. If the gap is too large, paste-in-hole processing may not provide acceptable solder fillets.
Technology options are coming on-line for selectively soldering thru-hole components in a mixed assembly. Laser soldering is one example. In my discussion of laser, I fully disclose that I am associated with laser soldering company BeamWorks. As there also are other valuable suppliers of laser soldering equipment, I am talking about laser systems in general in this article, and not about BeamWorks in particular.
Before we get into laser soldering DfM discussion, let us briefly discuss the laser soldering process, since it is relatively new. Laser soldering uses diode lasers to heat the component lead and PTH pad while automatically feeding solder wire to achieve the desired fillet. The wire has flux inside its core. This is a point-to-point soldering process similar to hand soldering, but it is faster and produces consistent quality, a key concern in hand soldering. Another laser soldering benefit, transitions from tin/lead to lead-free take minutes, requiring only that operators replace the solder wire spool.
Some high-end laser systems have built-in infrared (IR) sensors to monitor joint temperature during soldering. This IR sensor monitors the temperature of connections being made and automatically controls the duration of soldering to prevent either cold solder or board discoloration. Soldering duration generally is around 1 sec./joint, varying with surface finish, hole-to-lead-diameter ratio, component color, board thermal mass, and other factors. IR sensors allow precise process control by treating each joint according to its thermal requirement, using closed-loop feedback. Now here is the catch.
The IR sensor is sensitive to the color of component and board surfaces and soldermasks. It requires a minimum gap between the lead and hole diameter, similar to paste-in-hole processes. It is necessary, therefore, to follow certain DfM rules with laser soldering.
PTH diameter should not be much bigger than 20% of the lead diameter. The tighter gap between the lead and hole minimizes the amount of laser hitting the bottom of the component above the board surface. The objective is to heat the lead and not the bottom of the component.
If the PTH hole diameter is too large, it's optimal to have lighter components to reflect the laser away from the component body to the component lead where it is needed most. This will encourage good solder fillets in shortest possible soldering times. As a guideline, whenever possible, use components with lighter, preferably white, color rather than components with dark or black colors. When that is not possible, it is even more critical to maintain the smallest gap between the PTH hole and lead diameter.
Laser power also is sensitive to the color of board surface finish. Gold or electroless nickel immersion gold (ENIG) finishes will reflect laser more than a duller surface - tin or hot air solder leveling (HASL); hence, the laser will stay on for a longer time. Longer soldering times may result in board discoloration.
Lasers used in selective soldering typically have 2-mm diameters. It is better to have much bigger pad (annular ring) than normal; the pad will absorb the laser heat and protect the surrounding soldermask. If this is not possible, it is necessary to allow sufficient clearance between the pad and soldermask to prevent soldermask discoloration. Again, lighter, brighter, and shinier soldermasks are better than duller soldermasks, since they reflect laser heat to prevent discoloration.
It is helpful to have the same lead-length protrusion throughout the assembly. Fortunately, long lead protrusion is more acceptable with laser than wave - 2-2.5 mm for laser as opposed to ideally 1 mm in wave for bridge and icicle prevention. Some guidelines about spacing between taller and smaller components are in order as well, if the laser goes in at an angle. The greater the spacing between taller and smaller components, the lower the potential for shadowing from taller adjacent components. If extra spacing between components is not possible, attempt should be made during layout stage to place components of similar heights as neighbors.
There should be no flux on the board surface after the reflow process is completed for surface mount components. In other words, when the surface mount components are reflow soldered prior to selective laser soldering of thru-hole components, they should be cleaned properly. Why? Flux or paste in the sight of laser beam will burn. If the board is not cleaned after reflow, as would be the case for no-clean specs, it is recommended that you use low- or no-residue solder paste. This is helpful in preventing corrosion potential in the field, especially in humid environments.
Conclusion
Every process has its unique DfM requirements. Laser soldering is no exception. Its advantages over other selective soldering processes justify attention to laser DfM requirements. For example, there is no concern about copper dissolution at the PTH knee. Therefore, problems with internal and external barrel or trace cracking are eliminated, a common concern when dealing with lead-free solders in solder pots. Laser also avoids solder pot contamination, frequent pot cleaning, and disposal of dirty dross. Transitions from tin/lead to lead-free are quick and precise, especially important during the current transition period.
APPEARANCES:
APPEARANCES:
Ray Prasad regularly teaches in-depth SMT and BGA Design and Manufacturing and Lead-free Implementation courses in Portland, Oregon. He also teaches on-site classes for companies.
Ray Prasad is an SMT Editorial Advisory Board member, author of the textbook, Surface Mount Technology: Principles and Practice, and founder of the Ray Prasad Consultancy Group. Contact him at 12945 SW Glen Oak Place Beaverton, Ore 97007; (503) 628-1199; Fax: (503) 628-3399; smtsolver@rayprasad.com; www.rayprasad.com.
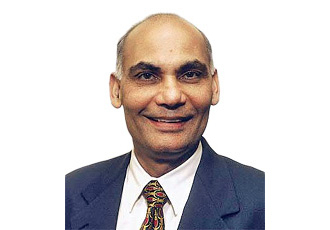
Registration is Open for SMT Course
Ray Prasad will be teaching his flagship SMT course: