SMT - AOI, Test and Repair: Waste of Money?
Any money spent on inspection, test and repair is wasted money. It adds only to cost and, hence, adversely impacts the bottom line. It does not add any value. So why do we need to perform these non-value added functions? The reasons are simple. As long as humans are involved, and to err is only human, we are stuck with inspection, test and rework. My modest goal in this column is to focus on ways to reduce the total cost of inspection (namely automated optical inspection [AOI]), test and repair.
Of these three non-value added functions, AOI is the only function that can be performed at any point in the line. Test and repair functions generally are performed at the end of the line. Also, AOI and test are somewhat interchangeable. Both these functions accomplish the same goal ¾ finding faults, although their capabilities may vary and they may be performed expensively or cheaply.
The third source of defects is the assembly process and equipment used in manufacturing. Let us look at the various manufacturing processes where the defects could come from. Before reflow, they could come from solder paste printing or placement machines. After reflow, they could come from the reflow oven itself. There are AOI systems on the market to perform inspection after any of these processes. If you have the budget, you can put an AOI system after each manufacturing process ¾ after printing, placement and reflow. However, this is not the way to achieve the lowest total cost.
AOI After Printing. To settle on the most cost-effective AOI strategy, ask the following general questions: "Which manufacturing process is easier to set up and control without AOI machines and which is not?" Also, do you want to prevent the problem from occurring or do you want to take the traditional approach and wait until the end of the line, inspect the defects and correct them before shipping the product to the customer?
There are only three major process steps in the SMT line ¾ paste printing, component placement and reflow. First, let us look at the printing process. Much had been written, illustrating the import of the printing process. Fortunately, it is the easiest process to control. The solder paste volume in paste printing is an important source of defects but easiest to prevent without spending money on AOI. This is because there are only two kinds of defects in a board that really matter ¾ opens and shorts or bridges. In my view, it is better to have shorts than opens because opens may escape, but shorts always will be caught. A board with bridges will never pass functional test, or any test. Also, shorts or bridges are easier to fix than opens. By designing stencil aperture correctly, and using a reasonable quality printer, you can control paste volume if you focus on getting about eight times more bridges than opens. This strategy also will prevent insufficient and open joints. Monitor shorts to open ratio and keep it at six or more.
AOI After Reflow. The reflow oven itself can cause defects. However, if you have taken the time to develop a unique profile for each product or product group, you can be sure that the reflow oven is not going to be your major concern. Also, AOI after reflow may have excessive false accepts and rejects. For example, it is difficult even for humans to decipher the subtle differences between cold solder, dewetting or non-wetting. How can an AOI system be expected to be accurate? Even if it is accurate, keep in mind that solder joint inspection after reflow is an after-the-fact step. It is too late to rework the defects you find at this stage. It not only adds to the total cost but adversely impacts solder joint reliability.
AOI After Placement. The third major source of defects is component placement. Placement machines have many fast, moving parts. Hence, they are the major source of problems. Additionally, they take long time to set up. It is not uncommon to incorrectly place a wrong reel, tube or tray, especially if the components look alike. But there is good news. Even inexpensive component placement verification AOI machines are effective in finding simple but common mistakes like wrong parts, part presence or absence, or wrong orientation or polarity. The AOI after placement machine is effective in performing complete first article inspection to make sure all feeders are set up correctly, the nozzles have not worn out and the vision system is working properly to place parts correctly. Also keep in mind that simple AOI systems for component verification are relatively inexpensive compared to AOI systems designed to inspect everything.
Because there generally are two or more pick-and-place machines in an SMT line, where should the AOI machine be placed to find the placement errors? If your AOI budget is limited, it may be better to place the system after the final placement machine to catch all placement errors. Additionally, because the last machine in the line places the fine-pitch components, it is important to catch all the fine-pitch-related problems. On a typical board, about half the defects are related to fine-pitch components even though there are only limited numbers of such components on a board.
So where do we go from here? I have nothing against placing an AOI machine after each manufacturing process; but this is not the way to reduce the total cost. In deciding whether to place the AOI system after printing, placement or reflow to minimize cost, an AOI after placement machine is the most cost-effective approach.
Of these three non-value added functions, AOI is the only function that can be performed at any point in the line. Test and repair functions generally are performed at the end of the line. Also, AOI and test are somewhat interchangeable. Both these functions accomplish the same goal ¾ finding faults, although their capabilities may vary and they may be performed expensively or cheaply.
In-circuit vs. Functional Test
Let us take test first. Taking a high-level view, there are two types of tests: in-circuit (also known as bed of nails or automated test equipment [ATE]) test (ICT) and functional test. ICT requires design stage planning so that sufficient test points can be inserted to allow bed-of-nails testing. The beauty of ICT is that it can diagnose the problem up to the component level, eliminating time spent in debugging the failed boards. ICT's drawback is that the equipment is expensive and the test fixtures for each board can cost anywhere from $10,000 to $40,000. This does not include the cost of developing the test programs. Functional test, on the other hand, does not require any test fixture or elaborate test setup. It simply is a go/no go test performed by plugging the board in the final system. Functional test's disadvantage comes in not knowing the nature of the problem when the board does fail. Depending on the technician's skill and experience, it could take anywhere from a few minutes to hours to find the source of the problem. One way to reduce the total cost of AOI, test and repair is to not use ICT and depend entirely on functional test to ensure your customer does not receive faulty boards. However, to enable complete reliance on functional test, your defects must be very low. Now we are back to the interrelationships between inspection, test and repair mentioned earlier. We need to ask the question: "Where do the defects come from and how effective are the AOI systems available on the market?"Major Defect Sources
Again taking a high-level view, there are three major defect sources, the first being design for manufacture (DFM). There is no AOI or test method that addresses DFM problems. More importantly, there are few companies that even feature in-house DFM. The blame for defects typically is placed on the assemblers because that is where the defects are discovered, even though the assembly processes have nothing to do with those defects. The second major source of defects is the quality of incoming materials such as the bare board, components, adhesive, solder paste, flux, etc. Again, like the DFM violations, no AOI or test method can help catch incoming material-related problems.The third source of defects is the assembly process and equipment used in manufacturing. Let us look at the various manufacturing processes where the defects could come from. Before reflow, they could come from solder paste printing or placement machines. After reflow, they could come from the reflow oven itself. There are AOI systems on the market to perform inspection after any of these processes. If you have the budget, you can put an AOI system after each manufacturing process ¾ after printing, placement and reflow. However, this is not the way to achieve the lowest total cost.
AOI After Printing. To settle on the most cost-effective AOI strategy, ask the following general questions: "Which manufacturing process is easier to set up and control without AOI machines and which is not?" Also, do you want to prevent the problem from occurring or do you want to take the traditional approach and wait until the end of the line, inspect the defects and correct them before shipping the product to the customer?
There are only three major process steps in the SMT line ¾ paste printing, component placement and reflow. First, let us look at the printing process. Much had been written, illustrating the import of the printing process. Fortunately, it is the easiest process to control. The solder paste volume in paste printing is an important source of defects but easiest to prevent without spending money on AOI. This is because there are only two kinds of defects in a board that really matter ¾ opens and shorts or bridges. In my view, it is better to have shorts than opens because opens may escape, but shorts always will be caught. A board with bridges will never pass functional test, or any test. Also, shorts or bridges are easier to fix than opens. By designing stencil aperture correctly, and using a reasonable quality printer, you can control paste volume if you focus on getting about eight times more bridges than opens. This strategy also will prevent insufficient and open joints. Monitor shorts to open ratio and keep it at six or more.
AOI After Reflow. The reflow oven itself can cause defects. However, if you have taken the time to develop a unique profile for each product or product group, you can be sure that the reflow oven is not going to be your major concern. Also, AOI after reflow may have excessive false accepts and rejects. For example, it is difficult even for humans to decipher the subtle differences between cold solder, dewetting or non-wetting. How can an AOI system be expected to be accurate? Even if it is accurate, keep in mind that solder joint inspection after reflow is an after-the-fact step. It is too late to rework the defects you find at this stage. It not only adds to the total cost but adversely impacts solder joint reliability.
AOI After Placement. The third major source of defects is component placement. Placement machines have many fast, moving parts. Hence, they are the major source of problems. Additionally, they take long time to set up. It is not uncommon to incorrectly place a wrong reel, tube or tray, especially if the components look alike. But there is good news. Even inexpensive component placement verification AOI machines are effective in finding simple but common mistakes like wrong parts, part presence or absence, or wrong orientation or polarity. The AOI after placement machine is effective in performing complete first article inspection to make sure all feeders are set up correctly, the nozzles have not worn out and the vision system is working properly to place parts correctly. Also keep in mind that simple AOI systems for component verification are relatively inexpensive compared to AOI systems designed to inspect everything.
Because there generally are two or more pick-and-place machines in an SMT line, where should the AOI machine be placed to find the placement errors? If your AOI budget is limited, it may be better to place the system after the final placement machine to catch all placement errors. Additionally, because the last machine in the line places the fine-pitch components, it is important to catch all the fine-pitch-related problems. On a typical board, about half the defects are related to fine-pitch components even though there are only limited numbers of such components on a board.
So where do we go from here? I have nothing against placing an AOI machine after each manufacturing process; but this is not the way to reduce the total cost. In deciding whether to place the AOI system after printing, placement or reflow to minimize cost, an AOI after placement machine is the most cost-effective approach.
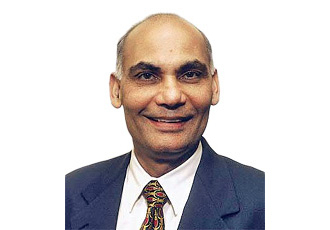
Registration is Open for SMT Course
Ray Prasad will be teaching his flagship SMT course: