SMT - Unresolved Issues in Lead-free Through-hole Soldering and Surface Finishes
Since we have been in SMT for more than two decades in high-volume production
Since we have been in SMT for more than two decades in high-volume production, one would think that we do not need to deal with through-hole components anymore. Not so. Through-hole is not going away for a long time to come for various reasons. The most common way to solder through-hole components en masse is through the wave soldering process. For tin-lead, the wave pot temperature for soldering through-hole components is generally maintained at 260°C.
When switching to lead-free, the pot temperature need not exceed 260°C although some people use as low as 255°C and some may go as high as 270°C. However, I do not believe you need to use higher than 265°C. Even though the peak reflow temperature for lead-free is much higher than that for tin-lead, the wave pot temperature for wave soldering lead-free component is essentially the same as it is for tin-lead. There are various reasons for staying close to 260°C.
Higher pot temperature has the increased potential for more board warpage and increased dissolution of copper from component leads and PCB surfaces. Even at 260°C due to increased concentration of tin in lead-free solder, the copper dissolution is much higher in lead-free solder than in tin-lead solder. This has various adverse effects. The lead-free wave pot is going to get contaminated faster and would require much more frequent analysis and dumping than was the case with tin-lead. The pot also will require more frequent clean up due to increased oxidation of tin in lead-free and sinking of heavier tin-copper intermetallic compound or IMC (Cu6Sn5) to the bottom of the pot.
The densities of lead-free, IMC and tin-lead solder are 7.39, 8.25 and 8.8 respectively. So in tin-lead solder, the IMC floats at the top since it is lighter than solder and hence gets skimmed off during clean up of dross. In lead-free solder, however, the IMC will tend to sink to the bottom since it is heavier than lead-free solder. If the IMC is not frequently removed from the pot, it will get intermixed with solder and may clog the baffles and channels in the pot, causing serious problems in proper functioning of the wave.
A higher rate of dissolution of copper in lead-free solder not only forces frequent pot maintenance, but it also has serious implications on solder joint reliability when the copper at the knee of the through-hole pad is totally dissolved. Some of the copper is dissolved during the initial wave soldering step. The remaining solder can disappear completely during subsequent rework, causing potentially an open joint.
What causes the copper to completely disappear during rework and not during initial wave soldering? During initial soldering, the dwell time is less than 10 seconds in the wave (5 seconds is more common) but during rework generally conducted in a mini solder pot the dwell time can be more than 60 seconds, which is long enough to completely remove the solder especially at the knee of the pads, causing an open solder joint. A more accurate way to describe this problem is that copper removal in the PTH knee in through-hole barrels during mini-pot rework is an erosion problem not just a dissolution problem.
Whenever there are technical issues like this in a new technology, there are companies with differing claims for coming to the rescue. This is especially true when it comes to selecting the right composition for lead-free solder for wave. The industry seems to be almost in agreement on SAC 305 for solder paste for reflow but there is no consensus when it comes to selection of solder composition for wave soldering.
Different interest groups are still jockeying for special advantage of their formulation. Most suppliers claim that their patented special formulation with traces of nickel or germanium or cobalt or some other secret elements does not dissolve copper as much as SAC solders and also cost less since they do not contain silver. This claim may be true somewhat for initial wave soldering but when it comes to rework or pot contamination, especially with IMC, none of the compositions can truly claim an advantage. You cannot reduce the dwell time too much during rework or change the density of IMC which will sink in the pot regardless of the solder composition used.
What is also worth noting is that all these alternative lead-free compositions do have about 10°C higher melting point than SAC 305 and will require higher pot temperature for good soldering results. Higher temperature will increase the potential for oxidation and board warpage. So you do need to do your detailed pro and con evaluation for any solder that you may decide to use. Do not expect any recommendation from industry organizations — you are on your own.
So our industry has a basic technological challenge as to how to deal with increased levels of wave pot contamination, increased dross formation and erosion of copper at the PTH knee. So what is really needed is an alternative rework system for through-hole that does not exist today. Anyone who can come up with a rework system that can reflow and remove through-hole components quickly without causing disappearance of copper at the PTH knee or causing internal barrel or trace cracking can truly claim an advantage. Does such a system exit today in the market place? No. Can such a system be developed? Yes, but it requires engineering and financial resources of users and equipment suppliers.
As for solving pot contamination and increased frequency of pot maintenance, the only way to achieve that is to switch to a selective soldering system. There are many suppliers of selecting soldering systems in the market place.
Another unsettled issue in lead-free is the selection of board surface finish. There are various surface finishes such as HASL, OSP and metal finishes such as silver and various incarnations of gold. Each has its issues and advantages; there is not a clear leader.
HASL — yes, the HASL that you thought had gone away — is being given another look by some major OEMs. Nothing solders like solder. Lead-free HASL is primarily tin with a small amount of copper to reduce the melting point of tin by 4°C or so — from 231° to 227°C and traces of other metals such as nickel, germanium or cobalt for grain refinement and multiple substantiated or unsubstantiated benefits.
The key issue with HASL has been uneven solder surface and potential solderability issues in areas with an extremely thin layer of solder. These issues have not been resolved. They were the reasons the industry moved away from HASL to alternative finishes such as OSP and other metal finishes in the first place. However, HASL is being reconsidered since OSP has hole fill issues in wave solder especially in thick boards and immersion silver will corrode in high sulfur environments.
The first one to claim the market share from HASL was OSP but it turned out to be a very fragile surface finish that requires careful handling, has hole fill issues especially when subjected to multiple reflows and does not provide good contact for ICT. Now high-temperature OSPs are showing up in the marketplace that do address the solderability issues in multiple reflows but still pose contact concerns in ICT unless those test pads are covered with solder.
Immersion silver and electroless nickel immersion gold or ENIG were to supposed to address the solderability and ICT contact issues of OSP but they have their own concerns such as planar micro voids in immersion silver and black pad in ENIG. Silver also has tarnishing concerns if not packed properly and corrosion issues in salty or sulfur containing environments. Such issues in immersion silver and ENIG are seen rarely and are related to the lack of plating process controls. Even so they do have the cloud hanging over them due to these concerns.
So now comes another surface finish that you may hear more about as the time goes on. It is the sibling of ENIG without the black pad concerns. It is called ENEPIG or electroless nickel electroless palladium gold. It is just like ENIG with an additional intermediate plating step with palladium, which is the magic metal between nickel and gold.
The only problem with ENEPIG is that it is not a very common surface finish and you may have to be the supplier on the leading edge to consider such a plating surface. And being on the leading edge is also being on the bleeding edge since what appears to be a fail safe surface finish in a lab environment may turn out to be a disaster in high-volume production. For example, immersion silver seemed to be the ideal surface finish during intensive initial evaluations by major OEMs but serious production issues cropped up in high-volume production especially in China where essentially everything is made these days. While China may be the king of low cost, make sure whatever you are trying to build does not require too much process control.
So which surface finish is the best? There is not any. You have to look at your application, your supplier’s capability and your relationship with them before selecting the right finish. In other words, we all have good job security with the host of technical issues brought by the lead-free changeover, the wisdom of which is an entirely different subject.
Ray Prasad is an SMT Editorial Advisory Board member and author of the textbook Surface Mount Technology: Principles and Practice and founder of the Ray Prasad Consultancy Group. Contact him at 12945 SW Glen Oak Place Beaverton, OR 97008; (503) 628-1199; Fax: (503) 628-3399; E-mail: smtsolver@rayprasad.com; Website: www.rayprasad.com.
Appearances: Looking for a lead-free implemention or SMT course? Ray Prasad will be teaching in-depth SMT and BGA Design and Manufacturing and Lead-free Implementation courses in Portland, Oregon. Visit www.rayprasad.com for course schedule and registration details.
Since we have been in SMT for more than two decades in high-volume production, one would think that we do not need to deal with through-hole components anymore. Not so. Through-hole is not going away for a long time to come for various reasons. The most common way to solder through-hole components en masse is through the wave soldering process. For tin-lead, the wave pot temperature for soldering through-hole components is generally maintained at 260°C.
When switching to lead-free, the pot temperature need not exceed 260°C although some people use as low as 255°C and some may go as high as 270°C. However, I do not believe you need to use higher than 265°C. Even though the peak reflow temperature for lead-free is much higher than that for tin-lead, the wave pot temperature for wave soldering lead-free component is essentially the same as it is for tin-lead. There are various reasons for staying close to 260°C.
Higher pot temperature has the increased potential for more board warpage and increased dissolution of copper from component leads and PCB surfaces. Even at 260°C due to increased concentration of tin in lead-free solder, the copper dissolution is much higher in lead-free solder than in tin-lead solder. This has various adverse effects. The lead-free wave pot is going to get contaminated faster and would require much more frequent analysis and dumping than was the case with tin-lead. The pot also will require more frequent clean up due to increased oxidation of tin in lead-free and sinking of heavier tin-copper intermetallic compound or IMC (Cu6Sn5) to the bottom of the pot.
The densities of lead-free, IMC and tin-lead solder are 7.39, 8.25 and 8.8 respectively. So in tin-lead solder, the IMC floats at the top since it is lighter than solder and hence gets skimmed off during clean up of dross. In lead-free solder, however, the IMC will tend to sink to the bottom since it is heavier than lead-free solder. If the IMC is not frequently removed from the pot, it will get intermixed with solder and may clog the baffles and channels in the pot, causing serious problems in proper functioning of the wave.
A higher rate of dissolution of copper in lead-free solder not only forces frequent pot maintenance, but it also has serious implications on solder joint reliability when the copper at the knee of the through-hole pad is totally dissolved. Some of the copper is dissolved during the initial wave soldering step. The remaining solder can disappear completely during subsequent rework, causing potentially an open joint.
What causes the copper to completely disappear during rework and not during initial wave soldering? During initial soldering, the dwell time is less than 10 seconds in the wave (5 seconds is more common) but during rework generally conducted in a mini solder pot the dwell time can be more than 60 seconds, which is long enough to completely remove the solder especially at the knee of the pads, causing an open solder joint. A more accurate way to describe this problem is that copper removal in the PTH knee in through-hole barrels during mini-pot rework is an erosion problem not just a dissolution problem.
Whenever there are technical issues like this in a new technology, there are companies with differing claims for coming to the rescue. This is especially true when it comes to selecting the right composition for lead-free solder for wave. The industry seems to be almost in agreement on SAC 305 for solder paste for reflow but there is no consensus when it comes to selection of solder composition for wave soldering.
Different interest groups are still jockeying for special advantage of their formulation. Most suppliers claim that their patented special formulation with traces of nickel or germanium or cobalt or some other secret elements does not dissolve copper as much as SAC solders and also cost less since they do not contain silver. This claim may be true somewhat for initial wave soldering but when it comes to rework or pot contamination, especially with IMC, none of the compositions can truly claim an advantage. You cannot reduce the dwell time too much during rework or change the density of IMC which will sink in the pot regardless of the solder composition used.
What is also worth noting is that all these alternative lead-free compositions do have about 10°C higher melting point than SAC 305 and will require higher pot temperature for good soldering results. Higher temperature will increase the potential for oxidation and board warpage. So you do need to do your detailed pro and con evaluation for any solder that you may decide to use. Do not expect any recommendation from industry organizations — you are on your own.
So our industry has a basic technological challenge as to how to deal with increased levels of wave pot contamination, increased dross formation and erosion of copper at the PTH knee. So what is really needed is an alternative rework system for through-hole that does not exist today. Anyone who can come up with a rework system that can reflow and remove through-hole components quickly without causing disappearance of copper at the PTH knee or causing internal barrel or trace cracking can truly claim an advantage. Does such a system exit today in the market place? No. Can such a system be developed? Yes, but it requires engineering and financial resources of users and equipment suppliers.
As for solving pot contamination and increased frequency of pot maintenance, the only way to achieve that is to switch to a selective soldering system. There are many suppliers of selecting soldering systems in the market place.
Another unsettled issue in lead-free is the selection of board surface finish. There are various surface finishes such as HASL, OSP and metal finishes such as silver and various incarnations of gold. Each has its issues and advantages; there is not a clear leader.
HASL — yes, the HASL that you thought had gone away — is being given another look by some major OEMs. Nothing solders like solder. Lead-free HASL is primarily tin with a small amount of copper to reduce the melting point of tin by 4°C or so — from 231° to 227°C and traces of other metals such as nickel, germanium or cobalt for grain refinement and multiple substantiated or unsubstantiated benefits.
The key issue with HASL has been uneven solder surface and potential solderability issues in areas with an extremely thin layer of solder. These issues have not been resolved. They were the reasons the industry moved away from HASL to alternative finishes such as OSP and other metal finishes in the first place. However, HASL is being reconsidered since OSP has hole fill issues in wave solder especially in thick boards and immersion silver will corrode in high sulfur environments.
The first one to claim the market share from HASL was OSP but it turned out to be a very fragile surface finish that requires careful handling, has hole fill issues especially when subjected to multiple reflows and does not provide good contact for ICT. Now high-temperature OSPs are showing up in the marketplace that do address the solderability issues in multiple reflows but still pose contact concerns in ICT unless those test pads are covered with solder.
Immersion silver and electroless nickel immersion gold or ENIG were to supposed to address the solderability and ICT contact issues of OSP but they have their own concerns such as planar micro voids in immersion silver and black pad in ENIG. Silver also has tarnishing concerns if not packed properly and corrosion issues in salty or sulfur containing environments. Such issues in immersion silver and ENIG are seen rarely and are related to the lack of plating process controls. Even so they do have the cloud hanging over them due to these concerns.
So now comes another surface finish that you may hear more about as the time goes on. It is the sibling of ENIG without the black pad concerns. It is called ENEPIG or electroless nickel electroless palladium gold. It is just like ENIG with an additional intermediate plating step with palladium, which is the magic metal between nickel and gold.
The only problem with ENEPIG is that it is not a very common surface finish and you may have to be the supplier on the leading edge to consider such a plating surface. And being on the leading edge is also being on the bleeding edge since what appears to be a fail safe surface finish in a lab environment may turn out to be a disaster in high-volume production. For example, immersion silver seemed to be the ideal surface finish during intensive initial evaluations by major OEMs but serious production issues cropped up in high-volume production especially in China where essentially everything is made these days. While China may be the king of low cost, make sure whatever you are trying to build does not require too much process control.
So which surface finish is the best? There is not any. You have to look at your application, your supplier’s capability and your relationship with them before selecting the right finish. In other words, we all have good job security with the host of technical issues brought by the lead-free changeover, the wisdom of which is an entirely different subject.
Ray Prasad is an SMT Editorial Advisory Board member and author of the textbook Surface Mount Technology: Principles and Practice and founder of the Ray Prasad Consultancy Group. Contact him at 12945 SW Glen Oak Place Beaverton, OR 97008; (503) 628-1199; Fax: (503) 628-3399; E-mail: smtsolver@rayprasad.com; Website: www.rayprasad.com.
Appearances: Looking for a lead-free implemention or SMT course? Ray Prasad will be teaching in-depth SMT and BGA Design and Manufacturing and Lead-free Implementation courses in Portland, Oregon. Visit www.rayprasad.com for course schedule and registration details.
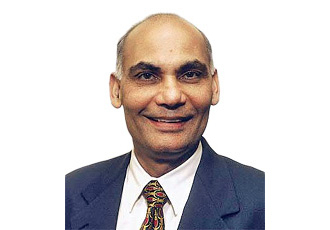
Registration is Open for SMT Course
Ray Prasad will be teaching his flagship SMT course: