Surface Mount Technology - Outline
Dedication
Foreword
Preface
Acknowledgments
About the Author
Part One - Introduction to Surface Mounting
Chapter 1 Introduction to Surface Mount Technology
1.0 Introduction
1.1 Types of Surface Mounting
1.2 Benefits of Surface Mounting
1.3 SMT Equipment Requiring Major Capital Investment
1.3.1 Pick-and-Place Equipment
1.3.2 Solder Paste Screen Printer
1.3.3 Curing/Baking Oven
1.3.4 Reflow Soldering Equipment
1.3.5 Cleaning
1.3.6 Wave Soldering Equipment
1.3.7 Repair and Inspection Equipment
1.4 When to Use Surface Mounting
1.5 Technical Issues in Surface Mounting
1.6 Trends in Surface Mounting
1.7 The Future
1.7.1 Chip-and-Wire Technology
1.7.2 Tape-Automated Bonding (TAB)
1.7.3 Flip Chip or Controlled Collapse Bonding
1.7.4 Multichip Module
1.8 Summary
References
Chapter 2 Implementing SMT In-House and at Subcontractors
2.0 Introduction
2.1 Setting the Implementation Strategy
2.2 Building the SMT Infrastructure
2.2.1 Developing the Internal SMT Infrastructure
2.2.1.1 Writing the Plan
2.2.1.2 Management Review
2.2.1.3 Hands-On Experience
2.2.1.4 Process Selection
2.2.1.5 Training
2.2.2 Influencing External SMT Infrastructure
2.3 Setting In-House Manufacturing Strategy
2.4 Selection of an Outside Assembly House
2.4.1 Reasons for Not Using Suppliers
2.4.2 Reasons for Using Suppliers
2.4.3 Evaluation and Qualification of Suppliers
2.4.4 Stages of Supplier Qualification
2.4.4.1 Preliminary Survey
2.4.4.2 Evaluation Status
2.4.4.3 Conditional Qualification Status
2.4.4.4 Approved Qualification Status
2.4.5 Supplier Rating
2.4.6 Questionnaires for Rating of Suppliers
2.4.6.1 Business Questions
2.4.6.2 Technology Questions
2.4.6.3 Manufacturing Questions
2.4.6.4 Quality Assurance Questions
2.4.7 Supplier Management or Partnership
2.5 Managing the Risk: Pilot to Production
2.6 Summary
Part Two - Designing with Surface Mounting
Chapter 3 Surface Mount Components
3.0 Introduction
3.1 Surface Mount Component Characteristics
3.2 Passive Surface Mount Components
3.2.1 Surface Mount Discrete Resistors
3.2.2 Surface Mount Resistor Networks
3.2.3 Ceramic Capacitors
3.2.4 Tantalum Capacitors
3.2.5 Tubular Passive Components
3.3 Active Components: Ceramic Packages
3.3.1 Leadless Ceramic Chip Carriers
3.3.2 Ceramic Leaded Chip Carriers (Preleaded and Postleaded)
3.4 Active Components: Plastic Packages
3.4.1 Small Outline Transistors
3.4.2 Small Outline Integrated Circuits (SOICs and SOPs)
3.4.3 Plastic Leaded Chip Carriers
3.4.4 Small Outline J Packages
3.4.5 Fine Pitch Packages
3.5 Ball Grid Arrays (BGAs)
3.5.1 Ceramic Ball Grid Array (CBGA)
3.5.2 Ceramic Column Grid Array (CCGA)
3.5.3 Plastic Ball Grid Array (PBGA)
3.5.4 Tape Ball Grid Array (TBGA)
3.6 Chip Scale Packaging
3.7 Major Issues in Components
3.7.1 Lead Coplanarity
3.7.2 Lead Configuration
3.7.2.1 Gull Wing
3.7.2.2 Balls (in BGA)
3.7.2.3 J Lead
3.7.2.4 Butt or I Lead
3.7.3 Standardization
3.8 Component Procurement Guidelines
3.9 Summary
Chapter 4 Substrates for Surface Mounting
4.0 Introduction
4.1 Glass Transition Temperature (Tg)
4.2 X, Y, and Z Coefficients of Thermal Expansion
4.3 Selection of Substrate Material
4.3.1 CTE Compatibility Considerations in Substrate Selection
4.3.2 Process Considerations in Substrate Selection
4.4 Ceramic Substrates
4.4.1 Porcelainized Steel Substrates
4.5 Constraining Core Substrates
4.5.1 Low CTE Metal Core Substrate
4.5.2 Graphite Epoxy Constraining Core Substrates
4.6 Compliant Layer Substrates
4.7 Glass Epoxy Substrates
4.7.1 Types of Glass Epoxy Substrate
4.7.2 Operating Temperatures for Glass Epoxy Boards
4.7.3 Fabrication of Glass Epoxy Substrates
4.8 Plating Processes
4.8.1 Copper Plating
4.8.2 Gold Plating
4.8.3 Nickel Plating
4.8.4 Lead-Tin Solder Plating
4.9 Alternative Coatings for Board Surfaces
4.10 Solder Mask Selection
4.10.1 Wet versus Dry Film Solder Masks
4.10.2 Photoimageable Solder Masks
4.11 Via Hole Cracking Problems in Substrates
4.12 Summary
Chapter 5 Surface Mount Design Considerations
5.0 Introduction
5.1 System Design Considerations
5.2 Package Drivers
5.2.1 PGA Drivers
5.2.2 Fine Pitch Drivers
5.2.3 Ball Grid Array (BGA) Drivers
5.2.4 Issues in Component Packaging
5.3 Real Estate Considerations
5.4 Manufacturing Considerations
5.5 Cost Considerations
5.5.1 Printed Circuit Board Cost
5.5.2 Component Cost
5.5.3 Assembly Cost
5.6 Thermal Considerations
5.7 Package Reliability Considerations
5.7.1 Package Cracking Mechanism
5.7.2 Solutions to Package Cracking
5.7.3 Moisture Sensitivity Classification for Package Cracking
5.8 Solder Joint Reliability Considerations
5.8.1 Solder Joint Reliability Tests
5.9 Interconnect Considerations
5.10 CAD Layout Considerations
5.11 Summary
Chapter 6 Surface Mount Land Pattern Design
6.0 Introduction
6.1 General Considerations for Land Pattern Design
6.2 Land Patterns for Passive Components
6.2.1 Land Pattern Design for Rectangular Passive Components
6.2.2 Land Pattern Design for Tantalum Capacitors
6.3 Land Patterns for Cylindrical Passive (MELF) Devices
6.4 Land Patterns for Transistors
6.5 Land Patterns for Plastic Leaded Chip Carriers
6.6 Land Patterns for Leadless Ceramic Chip Carriers
6.7 Land Patterns for Small Outline Integrated Circuits and R-Packs
6.8 Land Patterns for SOJ (Memory) Packages
6.9 Land Patterns for DIP (Butt Mount) Packages
6.10 Land Patterns for Fine Pitch, Gull Wing Packages
6.11 Land Pattern Design for Ball Grid Arrays (BGAs)
6.12 Land Pattern Design for TAB
6.13 Land Patterns for Solder Paste and Solder Mask Screens
6.14 Summary
Chapter 7 Design for Manufacturability, Testing, and Repair
7.0 Introduction
7.1 DFM Organizational Structure
7.2 General Design Considerations
7.3 Component Selection Considerations for Manufacturability
7.4 Soldering Considerations
7.5 Component Orientation Considerations
7.6 Interpackage Spacing Considerations
7.6.1 Assumptions in Interpackage Spacing Requirements
7.6.2 Interpackage Spacing Requirements
7.7 Via Hole Considerations
7.8 Solder Mask Considerations
7.9 Repairability Considerations
7.10 Cleanliness Considerations
7.11 Testability Considerations
7.11.1 Guidelines for ATE Testing
7.12 Summary
Part Three - Manufacturing with Surface Mounting
Chapter 8 Adhesive and Its Application
8.0 Introduction
8.1 Ideal Adhesive for Surface Mounting
8.1.1 Precure Properties
8.1.2 Cure Properties
8.1.3 Postcure Properties
8.2 General Classification of Adhesives
8.3 Adhesives for Surface Mounting
8.3.1 Epoxy Adhesives
8.3.2 Acrylic Adhesives
8.3.3 Other Adhesives for Surface Mounting
8.4 Conductive Adhesives for Surface Mounting
8.4.1 Electrically Conductive Adhesives
8.4.1.1 Anisotropic Electrically Conductive Adhesive
8.4.2 Thermally Conductive Adhesive
8.5 Adhesive Application Methods
8.5.1 Stencil Printing
8.5.2 Pin Transfer
8.5.3 Syringing
8.6 Curing of Adhesives
8.6.1 Thermal Cure
8.6.1.1 Thermal Cure Profile and Bond Strength
8.6.1.2 Adhesive Cure Profile and Flux Entrapment
8.6.2 UV/Thermal Cure
8.7 Evaluation of Adhesives with Differential Scanning Calorimetry
8.7.1 Basic Principles of DSC Analysis
8.7.2 DSC Characterization of an Epoxy Adhesive
8.7.3 DSC Characterization of an Acrylic Adhesive
8.8 Summary
Chapter 9 Solder Paste and Its Application
9.0 Introduction
9.1 Solder Paste Properties
9.1.1 Metal Composition
9.1.2 Metal Content
9.1.3 Particle Size and Shape
9.1.4 Flux Activators and Wetting Action
9.1.5 Solvent and Void Formation
9.1.6 Rheological Properties
9.1.6.1 Viscosity
9.1.6.2 Slump
9.1.6.3 Working Life and Tackiness
9.1.7 Solder Balls
9.1.8 Printability
9.2 Solder Paste Printing Equipment
9.2.1 Selecting a Printer
9.3 Solder Paste Printing Processes
9.3.1 Paste Printer Setup
9.3.2 Screen Printing
9.3.3 Stencil Printing
9.3.4 Screen Printing versus Stencil Printing
9.3.5 Dispensing
9.4 Paste Printing Defects
9.5 Paste Printing Variables
9.5.1 Solder Paste Viscosity
9.5.2 Print Thickness and Snap-Off
9.5.3 Squeegee Wear, Pressure, Hardness, Type, and Orientation
9.5.4 Print Speed
9.5.5 Mesh/Stencil Tension
9.5.6 Board Warpage
9.5.7 Etched, Laser Cut, and Electroformed Stencils
9.5.7.1 Chemically Etched Stencils
9.5.7.2 Laser Cut Stencils
9.5.7.3 Electroformed Stencils
9.6 Printing for Different Types of Components
9.6.1 Printing for Ball Grid Arrays
9.6.2 Printing for Fine Pitch and Ultra Fine Pitch
9.6.3 Printing for Through Hole in a Mixed Assembly
9.7 Summary
Chapter 10 Metallurgy of Soldering and Solderability
10.0 Introduction
10.1 Phase Diagrams
10.2 Metallization Leaching in Passive Surface Mount Components
10.3 Solder Alloys and Their Properties
10.4 Lead-Free Solder
10.4.1 Lead Replacement Elements
10.4.2 Lead-Free Solders and Their Properties
10.5 Solderability
10.5.1 Wetting
10.5.2 Nonwetting
10.5.3 Dewetting
10.6 Various Approaches for Ensuring Solderability
10.7 Solderability Test Methods and Requirements
10.7.1 General Solderability Test Requirements
10.7.1.1 Steam Aging Requirements
10.7.1.2 Flux and Solder Requirements
10.7.2 Dip and Look Test
10.7.3 Wetting Balance Test
10.7.4 Globule Test
10.8 Effect of Substrate Surface Finish on Solderability
10.9 Effect of Component Lead or Termination Finish on Solderability
10.9.1 Effect of Ni-Pd Lead Finish on Solderability
10.10 Summary
Chapter 11 Component Placement
11.0 Introduction
11.1 Manual Placement of Parts
11.2 Automated Placement of Parts
11.3 Selection Criteria for Placement Equipment
11.3.1 Maximum Substrate Size Handling Capacity
11.3.2 Maximum Feeder Input or Slot Capacity
11.3.3 Types and Sizes of Components
11.3.4 Placement Rate and Flexibility
11.3.5 Placement Accuracy/Repeatability
11.3.6 Vision Capability
11.3.7 Adhesive Dispensing Capability
11.3.8 Equipment Software Program
11.3.9 Service, Support, and Training
11.3.10 Other Important Selection Criteria
11.4 Selection of Feeders for Placement Equipment
11.4.1 Tape and Reel Feeders
11.4.2 Bulk Feeders
11.4.3 Tube or Stick Feeders
11.4.4 Waffle Packs
11.5 Available Placement Equipment
11.5.1 Equipment with High Throughput
11.5.2 Equipment with High Flexibility
11.5.3 Equipment with High Flexibility and Throughput
11.5.4 Equipment with Low Cost and Throughput but High Flexibility
11.6 Summary
Chapter 12 Soldering of Surface Mounted Components
12.0 Introduction
12.1 Wave Soldering
12.1.1 Design and Process Variables in Wave Soldering
12.1.2 Process and Equipment Variables in Wave Soldering
12.2 Developing a Wave Solder Profile
12.3 Types of Wave Soldering for Surface Mounting
12.3.1 Dual-Wave Soldering
12.3.2 Vibrating Wave Soldering
12.3.3 Modified Wave Soldering
12.4 Wave Soldering in an Inert Environment
12.5 Single-Step Soldering of Mixed Assemblies
12.6 Single-Step Soldering of Double-Sided SMT Assemblies
12.7 Vapor Phase Soldering
12.7.1 The Heat Transfer Mechanism in Vapor Phase Soldering
12.7.2 Solder Opens (Wicking)
12.8 Infrared Reflow Soldering
12.8.1 Heat Transfer Mechanism in IR Dominant Systems
12.8.2 Heat Transfer Mechanism in Convection Dominant Systems
12.8.3 Heat Transfer Mechanisms in Convection/IR Systems
12.8.4 Pros and Cons of Various IR Systems
12.9 IR Reflow Soldering in Nitrogen
12.10 Reflow Solder Profile Development
12.10.1 Preheat Zone
12.10.2 Soak Zone
12.10.3 Reflow Zone
12.10.4 Cooling Zone
12.11 Common Reflow Defects
12.11.1 Tombstoning and Part Movement
12.11.2 Thermal Shock on Components
12.11.3 Solder Mask Discoloration
12.12 Laser Reflow Soldering
12.13 Hot Bar Soldering
12.14 Hot Belt Reflow Soldering
12.15 Selecting the Appropriate Soldering Process and Equipment
12.16 Summary
Chapter 13 Flux and Cleaning
13.0 Introduction
13.1 Concerns in Surface Mount Cleaning
13.2 The Function of Flux
13.3 Considerations in Flux Selection
13.4 Flux Classification
13.4.1 Inorganic Fluxes
13.4.2 Organic Acid Fluxes
13.4.3 Rosin Fluxes
13.4.4 Low Residue or No-Clean Fluxes and Solder Pastes
13.4.4.1 Concerns About No-Clean Flux
13.5 Contaminants and Their Effects
13.5.1 Particulate Contaminants
13.5.2 Nonpolar Contaminants
13.5.3 Polar Contaminants
13.6 Major Considerations in the Selection of Cleaning Materials
13.6.1 Environmental Considerations
13.6.2 Other Considerations in Selecting Cleaning Materials
13.7 Cleaning Processes and Equipment
13.7.1 Organic Solvents (CFC Alternatives) and Cleaning Equipment
13.7.1.1 Batch Equipment for Organic Solvents
13.7.2 Semi-Aqueous Solvents and Cleaning Equipment
13.7.2.1 Semi-Aqueous Cleaning Equipment
13.7.3 Aqueous Cleaning Processes and Equipment
13.7.3.1 Deionization of Water for Cleaning
13.7.3.2 Aqueous Cleaning Equipment
13.8 Cleanliness Test Methods and Requirements
13.8.1 Visual Examination
13.8.2 Solvent Extraction
13.8.3 Surface Insulation Resistance (SIR)
13.8.3.1 SIR Measurement Test Conditions
13.8.3.2 Application of the SIR Test
13.9 Designing for Cleaning
13.10 Summary
Chapter 14 Quality Control, Inspection Repair, and Testing
14.0 Introduction
14.1 Statistical Quality Control
14.2 Application of SQC: A Case History
14.2.1 Implementing Statistical Process Control
14.3 Defects Related to Materials and Process
14.3.1 Substrate-Related Defects
14.3.2 Component-Related Defects
14.3.3 Adhesive-Related Defects
14.3.4 Defects Related to Solder Paste
14.3.5 Process-Related Defects
14.3.6 Design-Related Defects
14.4 Solder Joint Quality Requirements
14.4.1 Solder Joint Requirements for Rectangular Components
14.4.2 Solder Joint Requirements for Cylindrical Components
14.4.3 Solder Joint Requirements for Gull Wing Components
14.4.4 Solder Joint Requirements for J-Lead Components
14.4.5 Solder Joint Requirements for Butt Lead Components
14.4.6 Solder Joint Requirements for LCCCs
14.4.7 Generic Solder Joint Requirements
14.5 Solder Joint Inspection
14.5.1 Visual Inspection
14.5.2 Automated Inspection
14.5.2.1 Automated Laser Inspection
14.5.2.2 Transmission XRay and Scanned Beam Laminography Inspection
14.6 Repair Equipment and Processes
14.6.1 Repair Requirements
14.6.2 Soldering Irons for Surface Mount Repair
14.6.3 Hot Air Systems for Surface Mount Repair
14.6.4 BGA Repair
14.6.5 Rework Profiles
14.7 Assembly Testing
14.7.1 Fixtures for ATE Testing
14.7.2 Issues in ATE Testing
14.8 ISO 9000 Quality Standards and Certification
14.8.1 ISO 9000 Certification
14.8.2 Meeting ISO 9000 Standards
14.9 Summary
APPENDIX A
SURFACE MOUNT STANDARDS
APPENDIX B
DETAILED QUESTIONNAIRE FOR EVALUATING SMT EQUIPMENT: PICK-AND-PLACE (APPENDIX B1), SCREEN PRINTER (APPENDIX B2), AND REFLOW OVEN (APPENDIX B3)
APPENDIX C
GLOSSARY
INDEX
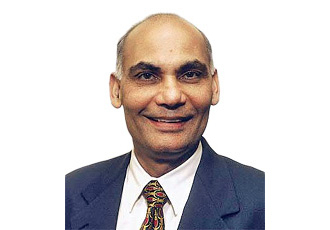
Registration is Open for SMT Course
Ray Prasad will be teaching his flagship SMT course: