SMT - Lead-free Reflow Profile Development: Part 1
With tin/lead there has been total industry unanimity about the composition of solder to be used — eutectic solder with 63% tin and 37% lead composition and a melting point of 183°C. With this composition, there was a big difference between the melting point and peak temperature (220°C). Even though it has been a recommended to maintain the temperature across the entire board between 210°–220°C, one easily could get away with maintaining a temperature of 190°–225°C and still achieve good reflow soldering results. This is about to change.
With the impending implementation of lead-free, SAC (Sn/Ag/Cu) solders have a melting point of about 220°C. Some components, such as aluminum electrolytic capacitors, put restrictions on maximum temperature and duration above 230°C.
To accommodate such constraints, the peak temperature of lead-free assemblies should be maintained between 230° and 245°C, a variation of only 15°C. This is about a 60% drop from the 35°C variation with tin/lead assemblies. The process window is further reduced if large components with high thermal mass are used with smaller and temperature-sensitive components. Large components with high thermal mass require higher peak temperatures for a longer duration of time, but smaller and temperature- sensitive components require lower temperatures for a shorter duration. This process window reduction will require tight process controls and a narrow temperature bandwidth across the board. Assembly houses may have a difficult time meeting such requirements, especially on complex boards without concerted time and effort in developing reflow profile. The solder profile is an important variable in the manufacturing process that impacts product yield significantly. Conveyor speed and panel temperatures are two variables in solder-profile development.
The solder profile is product specific and flux dependent. Different pastes require different profiles for optimum performance. Consult the paste supplier before developing the solder profile.
When developing the profile, we need the loaded board. We can start with a given belt speed and monitor the top-side board temperature using thermocouples. Most new reflow ovens have built-in thermocouples and software packages to record the thermal profile. Commercial hardware and software packages also are available to ease thermal profile development. Use of such profilers has been important in tin/lead assemblies. Now it is critical that they be used on each product to achieve good yield without exceeding temperature constraints of different types of components. There are four zones in a reflow profile. Here are some guidelines for achieving the desired shape in the four zones.
Preheat Zone. In the preheat zone, the temperature is 30°–175°C, and component suppliers generally recommend 2°–3°C/sec.ramp rate to avoid thermal shock to sensitive components such as ceramic chip resistors. This guideline is too conservative because the same capacitors are wave soldered where they go from preheat temperature of about 120°C to wave-pot temperatures of 260°C. The fast ramp rate increases the potential for solder balls. However, it is safe to use a 5°C/sec. ramp rate.
Soak Zone. This zone brings the entire board up to a uniform temperature. The ramp rate in this zone is slow, almost flat, when raising the temperature from 75°– 220°C. The consequences of being too high in the soak zone are solder balls and solder splatter due to excessive oxidation of paste. The soak zone also acts as the flux-activation zone for solder paste. The purpose of the long soak zone is to minimize voids, especially in BGAs. It also is common practice not to use the soak zone, but ramp the temperature steadily from preheat zone to peak reflow. However, the likelihood of voids is increased when ramping steadily to the peak reflow temperature.
Reflow Zone. In this zone, boards may char or burn if the temperature is too high. If the temperature is too low, cold and grainy solder joints will result. The peak temperature in this zone should be high enough for adequate flux action and good wetting. However, it should not be so high as to cause component or board damage, discoloration, or charring of the board. The peak temperature in this zone should be 230°–245°C for lead-free. The time above liquidus (TAL) should be 30-60 seconds. Extended duration above the solder melting point or TAL will damage temperature-sensitive components. It also results in excessive intermetallic growth, which makes the solder joint brittle and reduces solder joint fatigue resistance.
Cooling Zone. The cooling rate of the solder joint after reflow also is important. The faster the cooling rate, the smaller the solder grain size and the higher the fatigue resistance. The cooling rate should be as fast as possible. However, there is no control on the cooling rate other than ensuring that the cooling fans are operational. If they are not, the cooling rate will be slow, increasing grain size and causing weaker solder joints.
Achieving the desired time, temperature, and uniformity of temperature across the board in all four zones within 5°–10°C is vital in developing a reflow profile. Adjust the panel settings and belt speed until these objectives are met. The right profile with tight bandwidth is like using a good design for manufacturing (DFM).
SMT - Lead-free Reflow Profile Development: Part 2
With the impending implementation of lead-free, SAC (Sn/Ag/Cu) solders have a melting point of about 220°C. Some components, such as aluminum electrolytic capacitors, put restrictions on maximum temperature and duration above 230°C.
To accommodate such constraints, the peak temperature of lead-free assemblies should be maintained between 230° and 245°C, a variation of only 15°C. This is about a 60% drop from the 35°C variation with tin/lead assemblies. The process window is further reduced if large components with high thermal mass are used with smaller and temperature-sensitive components. Large components with high thermal mass require higher peak temperatures for a longer duration of time, but smaller and temperature- sensitive components require lower temperatures for a shorter duration. This process window reduction will require tight process controls and a narrow temperature bandwidth across the board. Assembly houses may have a difficult time meeting such requirements, especially on complex boards without concerted time and effort in developing reflow profile. The solder profile is an important variable in the manufacturing process that impacts product yield significantly. Conveyor speed and panel temperatures are two variables in solder-profile development.
The solder profile is product specific and flux dependent. Different pastes require different profiles for optimum performance. Consult the paste supplier before developing the solder profile.
When developing the profile, we need the loaded board. We can start with a given belt speed and monitor the top-side board temperature using thermocouples. Most new reflow ovens have built-in thermocouples and software packages to record the thermal profile. Commercial hardware and software packages also are available to ease thermal profile development. Use of such profilers has been important in tin/lead assemblies. Now it is critical that they be used on each product to achieve good yield without exceeding temperature constraints of different types of components. There are four zones in a reflow profile. Here are some guidelines for achieving the desired shape in the four zones.
Preheat Zone. In the preheat zone, the temperature is 30°–175°C, and component suppliers generally recommend 2°–3°C/sec.ramp rate to avoid thermal shock to sensitive components such as ceramic chip resistors. This guideline is too conservative because the same capacitors are wave soldered where they go from preheat temperature of about 120°C to wave-pot temperatures of 260°C. The fast ramp rate increases the potential for solder balls. However, it is safe to use a 5°C/sec. ramp rate.
Soak Zone. This zone brings the entire board up to a uniform temperature. The ramp rate in this zone is slow, almost flat, when raising the temperature from 75°– 220°C. The consequences of being too high in the soak zone are solder balls and solder splatter due to excessive oxidation of paste. The soak zone also acts as the flux-activation zone for solder paste. The purpose of the long soak zone is to minimize voids, especially in BGAs. It also is common practice not to use the soak zone, but ramp the temperature steadily from preheat zone to peak reflow. However, the likelihood of voids is increased when ramping steadily to the peak reflow temperature.
Reflow Zone. In this zone, boards may char or burn if the temperature is too high. If the temperature is too low, cold and grainy solder joints will result. The peak temperature in this zone should be high enough for adequate flux action and good wetting. However, it should not be so high as to cause component or board damage, discoloration, or charring of the board. The peak temperature in this zone should be 230°–245°C for lead-free. The time above liquidus (TAL) should be 30-60 seconds. Extended duration above the solder melting point or TAL will damage temperature-sensitive components. It also results in excessive intermetallic growth, which makes the solder joint brittle and reduces solder joint fatigue resistance.
Cooling Zone. The cooling rate of the solder joint after reflow also is important. The faster the cooling rate, the smaller the solder grain size and the higher the fatigue resistance. The cooling rate should be as fast as possible. However, there is no control on the cooling rate other than ensuring that the cooling fans are operational. If they are not, the cooling rate will be slow, increasing grain size and causing weaker solder joints.
Achieving the desired time, temperature, and uniformity of temperature across the board in all four zones within 5°–10°C is vital in developing a reflow profile. Adjust the panel settings and belt speed until these objectives are met. The right profile with tight bandwidth is like using a good design for manufacturing (DFM).
SMT - Lead-free Reflow Profile Development: Part 2
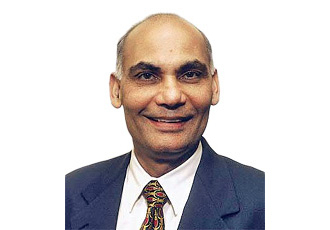
Registration is Open for SMT Course
Ray Prasad will be teaching his flagship SMT course: